Come abilitare la IV rivoluzione industriale? Qualche esempio pratico…
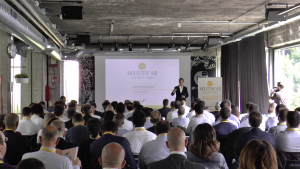
Per Industry 4.0 si intende un processo che traghetta l’azienda verso una produzione industriale del tutto automatizzata in cui le nuove tecnologie digitali si integrano perfettamente con il mondo fisico e ne aumentano esponenzialmente le performance. Tutto ciò prende il nome di quarta rivoluzione industriale, ma è realmente in atto oggi? La nostra esperienza ci dice che non basta un nuovo macchinario per fare Industria 4.0: oggi le tecnologie abilitanti ci sono, si può per esempio disporre del controllo da remoto delle performance, di un’attività di manutenzione predittiva, di funzioni di picking e di assemblaggio digitali, dell’additive manufacturing. Oggi l’evoluzione della tecnologia ci offre la possibilità di comprare macchinari nuovi che introducono concetti di industria 4.0 con componenti di ultima generazione oppure di introdurre su macchinari esistenti dei sensori che raccolgono dati a cui prima non si aveva accesso. O ancora, è possibile realizzare un’app per device tablet o mobile phone con cui tenere sotto controllo i parametri della linea produttiva. Ma tutte queste implementazioni rimangono solo esperienze contenute se nell’azienda non è presente un terreno fertile e una cultura pronta ad accogliere e favorire l’innovazione.
Il tradizionale business model del settore produzione sta cambiando, dunque, ma prima di definirla un fenomeno in atto, la quarta rivoluzione industriale va meditata e preparata: solo avendo alle spalle solidi processi di base, efficaci ed efficienti, infatti, è possibile beneficiare dei potenziali vantaggi della digitalizzazione del manufacturing. Ecco perché riteniamo che Lean e Digital siano sinergici e che laddove l’approccio Lean genera il cambiamento verso l’eccellenza di processi e prodotti, gli strumenti Digital ne amplificano e velocizzano gli effetti. Poi, quello che può fare la differenza, è creare una nuova cultura aziendale pronta ad affrontare l’innovazione.
A tal proposito, due considerazioni interessanti sono che nella loro vita privata, le persone sono molto più digitali rispetto al loro ambiente professionale, utilizzano la tecnologia quotidianamente per prenotare viaggi, per informarsi su cosa accade dall’altra parte del mondo, per fare acquisti online, ma in ufficio si limitano all’utilizzo di pochi programmi abituali. Soprattutto in Italia. La seconda è che nei luoghi in cui si genera la ricchezza del Paese stanno venendo meno le principali fonti di innovazione, ossia i giovani.
Nell’ultimo quarto di secolo, dai luoghi di lavoro sono sparite 3,6 milioni di persone di meno di 35 anni (erano quasi 9 milioni, sono poco più di cinque), sono apparse 4,2 milioni di persone in più la cui età supera i 45 anni, il numero dei lavoratori attivi fra i 55 e i 64 anni è raddoppiato da due a quattro milioni, tanto che il Fondo monetario internazionale stima che in Italia nel 2020 un quinto degli occupati sarà in questa fascia d’età. Eppure non sarà un caso se dall’ultima classifica stilata da Forbes, su 195 super ricchi, 56 sono under 40, il settore in cui i giovani miliardari investono di più è quello della tecnologia e dei 56, 23 super ricchi hanno creato la propria ricchezza a partire da investimenti o da scoperte in questo ambito.
Qualche mese fa, ho letto su Corriere che Marco Palmieri, per continuare a far crescere la sua azienda, aveva pensato di collegare le sue borse e valigie alla rete. Il fondatore e amministratore delegato di Piquadro si era rivolto a numerosi specialisti che gli avevano illustrato molte funzioni digitali, ma nessuna che facesse funzionare meglio uno zaino o una valigia in aeroporto. Poi un giorno si era confrontato alla macchinetta del caffè, con alcuni suoi dipendenti fra i 20 e i 30 anni. Fu la svolta: in poco tempo quei ragazzi idearono un’app per allucchettare le valigie e un sistema di sensori collegati allo smartphone per pesarle o segnalarne la posizione. Non erano specialisti del digitale, erano semplicemente giovani al lavoro. Servirebbe dunque un’ondata di freschezza all’interno delle aziende, un incremento di nuove generazioni che, cresciute parallelamente allo sviluppo digitale, possano affiancare i più senior e contaminare loro e l’ambiente lavorativo con il loro vigore innovativo, con la loro predisposizione a usare la tecnologia. E per accelerare i tempi, sarebbe poi utile lasciarle più libere di dare il proprio audace contributo.
CASI CONCRETI
Baltur (Gruppo Fava) progetta, produce e propone soluzioni intelligenti per il riscaldamento, la climatizzazione e le applicazioni industriali e di processo. 61 milioni di euro di fatturato nel 2016.
- PROGETTO: SmartKart, la digitalizzazione del processo di asservimento linea di montaggio The Best
Il progetto di digitalizzazione della linea, denominato SmartKart, prevede l’inserimento a bordo di specifici carrelli, di un tablet interfacciato in tempo reale al gestionale aziendale. In tal modo, quando l’operatore di magazzino, da noi denominato “kittatore”, preparerà i componenti della distinta base di assemblaggio di un bruciatore, oltre alla verifica visiva e a quella con bar code, avrà con il tablet la possibilità di vedere immagini esclusive e informazioni specifiche del componente da prelevare da confrontare poi con il suo terminale radio, per avere la matematica certezza di aver prelevato quello giusto. Tutto questo sistema sarà poi collegato al processo di fabbricazione in linea. E’ stato previsto infatti un secondo step che riguarda la creazione di una struttura informativa interna dove ogni carrello avrà un orario di partenza e un orario di arrivo (molto simile ai tabelloni degli aeroporti o delle stazioni ferroviarie). L’area carrelli verrà quindi dotata di un monitor fisso dove verrà segnalato quale SmartKart prelevare da portare a bordo linea, oppure quale Smarkart è libero da utilizzare. La terza fase del progetto infine prevede che anche l’operatore che assembla il componente avrà a bordo della sua postazione di lavoro, un ulteriore tablet che gli dirà esattamente il codice componente da prelevare e gliene mostrerà un’immagine per garantire che sia quello giusto. Cosa comporta tutto ciò? Comporta che nel caso in cui un cliente segnali un’anomalia o un cattivo funzionamento di un bruciatore, Baltur avrà la mappatura di tutto il processo di logistica e fabbricazione che gli permetterà di intraprendere tempestivamente le più appropriate azioni correttive.
D.V.P. Vacuum Technology S.p.A compete oggi a livello mondiale nel settore delle pompe per vuoto e compressori, ha sede a San Pietro in Casale (Bologna) e quattro filiali in Europa. Fatturato circa 15 milioni di euro.
- PROGETTO: Vuoto intelligente, la pompa 4.0. La prima piattaforma cloud integrata per il remote controlling dei sistemi per il vuoto
StarLink è un dispositivo innovativo con cui si possono monitorare e controllare i parametri significativi della pompa per vuoto come le temperature di lavoro, la pressione dell’impianto, le ore di esercizio della pompa, la corrente assorbita dal motore, il livello dell’olio e il livello di intasamento del filtro disoleatore. Questi parametri sono disponibili e quindi monitorabili su una piattaforma web che riceve il segnale da StarLink direttamente su pc, tablet o smartphone. StarLink permette di evitare fermi-macchina imprevisti, pianificare la manutenzione e, grazie ad alert preventivi è possibile supervisionare i processi e controllarne i costi. StarLink è disponibile sulle Pompe per vuoto e Compressori DVP con un design completamente rinnovato.
GEA è fra i principali fornitori tecnologici nell’industria alimentare e in una vasta gamma di altre industrie di processo. GEA ha chiuso il 2015 con un fatturato consolidato di più di 4,6 miliardi di euro, di cui più del 70% generato nel settore alimentare, un settore che registra una crescita a lungo termine.
- PROGETTO: Dalla manutenzione predittiva al Machine to Machine per il miglioramento delle performance. Il caso GEA
Hanno sviluppato un sistema di monitoraggio sulle loro macchine, in particolare sulla famiglia degli omogeneizzatori – di manutenzione predittiva, con l’obiettivo di anticipare i possibili malfunzionamenti invece che reagire ai guasti. Oltre a ciò, poiché questi omogeneizzatori sono composti da due sistemi che provengono da due stabilimenti diversi, hanno fatto in modo di far parlare le macchine fra loro (machine to machine) e farle interagire automaticamente attraverso criteri di simulazione che riducono lo scarto e migliorano le performance del prodotto
Benefici: riduzione costante dei costi di funzionamento della macchina. Uso della macchina nelle sue migliori condizioni operative e miglioramento dell’efficienza. Aumento dell’affidabilità e disponibilità dei macchinari.
di Michele Bonfiglioli
Contenuti correlati
-
Omron: efficienza e robotica, un binomio vincente
Il ritardo degli investimenti in tecnologie innovative comporta numerosi rischi, ma soprattutto ostacola l’efficienza. Peter Lange, business development manager robotics presso Omron Electronics spiega perché le aziende che sono ancora titubanti sui loro piani in ambito robotico...
-
Tecnologie a 2 conduttori
Il ruolo delle tecnologie a 2 conduttori per affrontare le sfide dell’Industria 4.0: Single Pair Ethernet e Advanced Physical Layer Ora che le sfide dell’Industria 4.0 stanno arrivando anche nell’automazione di processo, i protocolli di comunicazione industriale...
-
Reti come ‘commody’ – versione integrale
Le reti industriali, con la loro capacità di veicolare una notevole mole di informazioni attuando la convergenza IT-OT, sono alla base della transizione gemella, digitale e green. Sebbene la loro presenza sia a volte ‘scontata’, la loro...
-
Come ottimizzare la catena di produzione?
I dati raccolti grazie all’Industria 4.0 possono essere utilizzati sotto diverse forme, per migliorare numerosi aspetti del processo produttivo Negli ultimi anni, l’integrazione delle tecnologie digitali nell’industria ha raggiunto un livello senza precedenti, merito anche dell’avvento dell’Industria...
-
Il dato diventa valore
Nell’era dell’Industria 4.0, per trasformare i dati in valore, Ingranaggi Moreali Mario ha scelto di utilizzare la X Platform di Exor International Nell’era dell’Industria 4.0, l’automazione industriale e l’uso intelligente dei dati sono elementi chiave per migliorare...
-
Analisi dei dati nell’industria: contesto nazionale
Oggigiorno le organizzazioni che sono in grado di raccogliere le informazioni e utilizzarle in modo efficace possiedono un forte vantaggio competitivo sul mercato Il dato è l’elemento più prezioso al mondo, infatti è il risultato di un...
-
Come uso i dati?
Nella maggior parte dei casi le fabbriche intelligenti non nascono da zero, hanno siti produttivi già esistenti, ma una transizione e un’evoluzione sono sempre possibili proprio grazie alle nuove tecnologie Con la convergenza dei sistemi IT/OT, le aziende...
-
Dall’assistenza remota all’IIoT
Grazie all’impiego dei gateway Ewon Flexy di HMS Networks, Omet, punto di riferimento in ambito di macchine per la stampa e il converting di etichette e imballaggi flessibili, è diventata più efficiente “La prima macchina la vende...
-
Il duplice ruolo dell’AI nei data center on-premise
Molte aziende oggi desiderano sfruttare la potenza dell’intelligenza artificiale e i data center rappresentano una piattaforma capace di supportare queste ambizioni. Tuttavia, per ottenere prestazioni ottimali è necessario disporre di un’infrastruttura e di un’architettura di rete ben progettate. L’AI...
-
I dati? Sono acquisiti in modo sicuro e affidabile
Grazie a soluzioni Softing è possibile un’integrazione sicura e centralizzata dei dati e la gestione del modello informativo per OPC-UA e SAP Business Suite Un importante gruppo industriale internazionale, specializzato nella produzione e distribuzione di sistemi di filtraggio...