
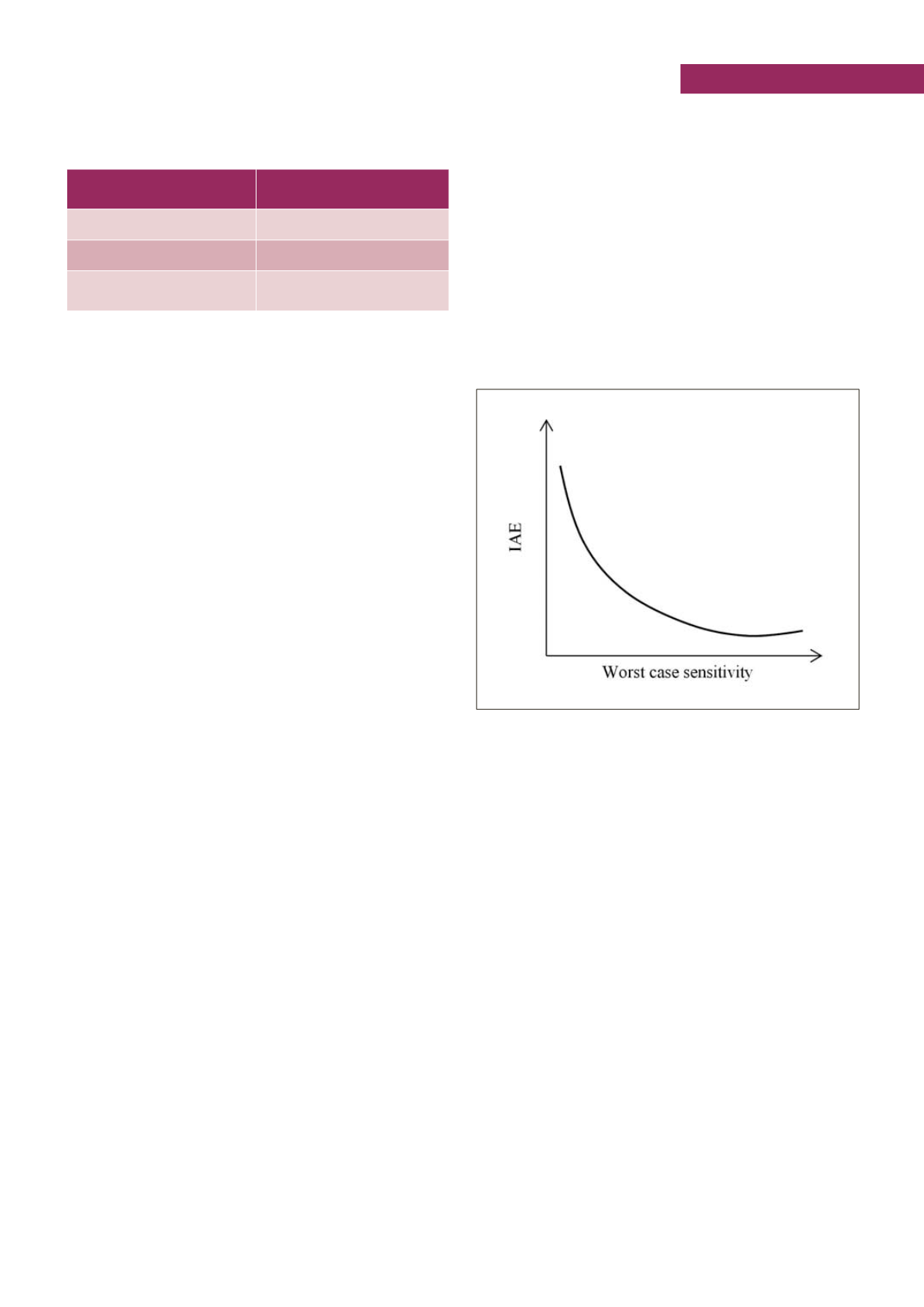
CONTROLLO
tecnica
Automazione e Strumentazione
Marzo 2018
89
tion to the disturbance means high overshoot in the response
to setpoint step change. This is very common when zero-pole
cancellation tuning is applied: the cancellation works fine for
the tracking task but the poles of the process are still there in the
transfer function between the load disturbance and the process
variable. The typical situations are summarized in the table.
Trade-off between performance and robustness
Another important trade-off is the one between performance and
robustness. The robustness is a measure of how much the con-
troller can tolerate changes in the process transfer function; more
specifically, in its gain and in its phase lag.
Also in this case there are some useful parameters which can be
used as design criteria for robustness:
- The gain margin is a measure of how much the process gain
can change (typically, increase) before the closed loop system
become unstable; the control theory says it is the amount of
gain increase or decrease required to make the loop gain unity
at the frequency where the phase angle is -180°; more accu-
rately, it is the maximum factor by which the process gain can
be multiplied before the closed loop become unstable.
- The phase margin (
m
) is a measure of how much the pro-
cess phase can change (typically, increase) before the closed
loop system become unstable; the process critical phase
c
could be increased because of an additional delay (dead-
time, due, for example to friction in the valve) or because
the process lag decrease (due, for instance, to a change in
the fluid properties or in the reaction speed); from the con-
trol theory the maximum delay that could be tolerated by the
loop is =
m
/
c
(where is the critical pulse corresponding to
the point where the Nyquist diagram enter in the unit circle).
Furthermore, it’s interesting to remark that when the closed
loop system starts being represented by a second order
oscillating system, its damping is somehow proportional to
the phase margin.
One interesting single parameter for evaluating the robustness is
the so called worst case sensitivity, given by the shorter distance
from the Nyquist diagram to the real point -1; this maximum sen-
sitivity is strictly related to the gain and phase margin through
some simple inequalities.
Through this single parameter it’s not difficult represent-
ing the trade-off between performance and robustness as it
happens in the figure (which is referred to a simple specific
FOPDT process); of course the trade-off does not continue so
much on the right because as soon the Nyquist diagram start
approaching to (-1, 0i) the behavior becomes oscillating and
IAE increases again.
Additional considerations should be made about the measure-
ment noise filtering and the control action effort. The closed loop
system acts more or less ad a low-pass filter with unit gain and
bandwidth equal to [0
c
]; therefore
c
should be set high enough
to allow fast setpoint changes and quick reaction to disturbances
but not so much to let the measurement noise affect the control
action: for not stressing or saturate the actuator, the controller
C(j ) should not have high values for >
c
. So it clear that we
have a trade-off again.
Solutions and Conclusions
In order to resolve the trade-off, some countermeasures can be
adopted. One solution is implementing a
two degree of free-
dom
(2DoF) controller where the ordinary PID parameters can
be tuned for good disturbance rejection but an additional set-
point weight allows to attenuate the overshoot in the setpoint
following task. Where the 2DoF algorithm is not available, set-
point changes should be ramp instead of step.
Another solution is employing
different sets of PID parameters
depending by the task or the situation to cope with. The default
set should be for providing an effective reaction to the unpre-
dictable disturbances; then a different set can be recalled any
time setpoint change is given by the operator or by a sequence
currently under execution. When it is known the plant unit is
going to work in unusual conditions different from the nominal
process design, then a set of robustness-oriented PID parame-
ters can be copied in the controller memory.
The PID algorithm is one of the simplest solutions to control
problems but it cannot provide effective results for different
kind of performance and goals; it is worth focusing on
the more
relevant task
and selecting the set of parameters more appro-
priate for it; alternatively some a bit more complex techniques
can be implemented in order to make the PID controller effec-
tive in different operating conditions.
Example Typical Trade-off between robustness and performance
Setpoint following
(tracking problem)
Load disturbance rejection
(regulation problem)
Slow with no overshoot
Sluggish
Fast with poor overshoot
Quiet reaction with no overshoot
Fast with large overshoot
and oscillations
Fast reaction with poor overshoot
Typical situations occurring during PID tuning procedures