
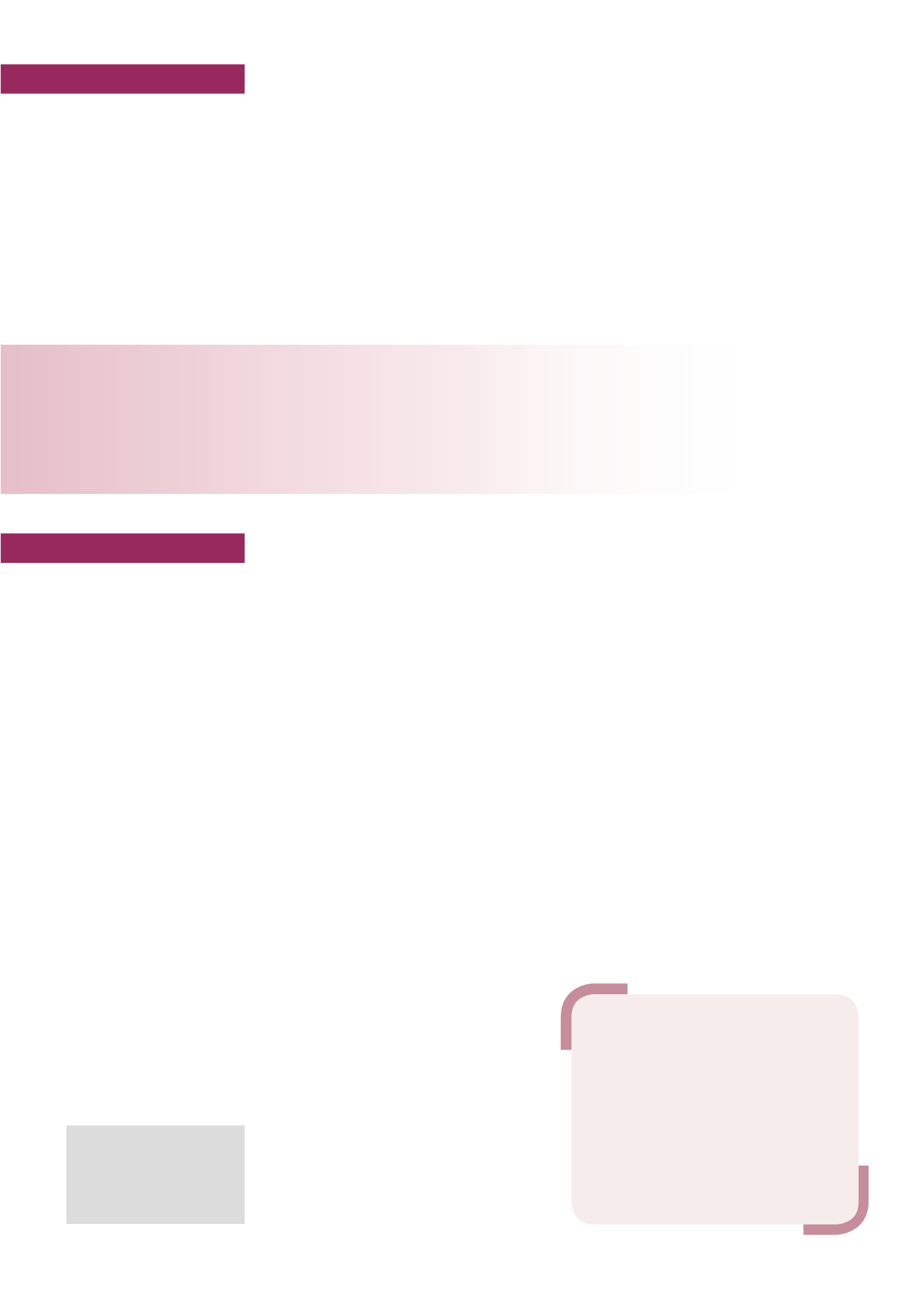
CONTROLLO
tecnica
Marzo 2018
Automazione e Strumentazione
88
When considering a control task, different goals can be considered. By employing a
simple linear PID controller the related design specifications cannot be simultaneously met:
one good behavior in one direction may mean poor performance in another one. It is
worth keeping this in mind and focusing on the main task, possibly by introducing some
quantitative performance indexes.
Massimiliano Veronesi
The trade-off among
different control loop performances
Despite some kind of advanced control algo-
rithms can be successfully implemented (think
about multivariable predictive control), simple
PID controllers
are still in charge of more than
90% of the industrial loops and act as base layer
for the more sophisticated techniques. Thanks to
their attractive cost/benefit ratio, PID algorithms
are widely employed; however their benefits are
not always fully exploited and their performance
could be improved. In this context it is worth
having a clear idea of which kind of performance
has to be addressed as first.
When considering a control task, not a few goals
could come in mind: think about setpoint refer-
ence following, disturbance rejection, control
effort saving, robustness versus different oper-
ating conditions. These goals cannot be inde-
pendently achieved at the same time : on the
other hand, good behavior in one direction may
mean poor performance in another one. Each
goal can be translated into design specifications
and specific indexes can measure the perfor-
mance of the PID controller.
Trade-off between tracking
and regulation
The setpoint following task can be addressed
through the crossover frequency of the loop
transfer function (i.e. the product of the transfer
function of the process and the one of the con-
troller): higher crossover frequency (i.e. the one
corresponding to the point where the Nyquist dia-
gram enters in the unit circle) means faster closed
loop response. When tuning one standard (i.e.
one degree of freedom) PID controllers, it is hard
to achieve good tracking and fast disturbance
rejection at the same time. Assuming the control
bandwidth is fixed, faster disturbance rejection
requires more gain inside the bandwidth, which
can only be achieved by increasing the slope near
the crossover frequency. Because a larger slope
means getting closer to the critical (-1, 0i) point,
this typically comes at the expense of more over-
shoot in the response to setpoint changes.
These parameters may be not so familiar to the
operators who is typically more used to time-do-
main interpretations; therefore rising time, set-
tling time and maximum overshoot are com-
monly considered; a nice kind of ‘summarizing’
quantity is represented by the integral of the abso-
lute errors (IAE) which can be low only if the
response is quite fast but not so much oscillating.
However it is worth stressing that the closed
loop transfer function between the setpoint
reference ad the error is different from the one
between the load disturbance and the error;
therefore a low IAE in fast tracking task leads
to sluggish behavior with high IAE in the load
disturbance rejection; viceversa a quick reac-
L’AUTORE
M. Veronesi, Product Marketing
Manager, Process Control & Safety
Systems, Yokogawa Italy
MAKING A PID CONTROLLER EFFECTIVE UNDER DIFFERENT CONDITIONS
Il compromesso tra diverse
prestazioni del controllo
Quando si considera un compito di controllo, vanno presi in esame
differenti obiettivi. Utilizzando un semplice regolatore PID lineare, le
specifiche di progetto possono non essere raggiungibili simultanea-
mente: il buon comportamento in una direzione può implicare delle
prestazioni scarse in un’altra. Vale la pena tenere presente questo e
concentrarsi sul compito principale, possibilmente introducendo degli
indici di prestazione quantitativi.