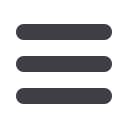

AUTOMAZIONE OGGI 395
SOLUZIONI SOFTWARE PER L’INDUSTRIA 113
controllo
S
SI
dal sistema da controllare. Il
bus seriale RS-485 con proto-
collo Modbus è il metodo più
diffuso per interagire con con-
trollori e PLC e rilevare i loro
stati operativi, ma può anche
utilizzare altri protocolli e per-
sino leggere direttamente lo
stato di segnali digitali. La rac-
colta di informazioni è la fase
essenziale in cui avviene anche
la loro ‘normalizzazione’. Per
normalizzazione si intende la
trasformazione di un dato numerico privo di significato, in
una misura. Come è noto una misura è dotata di una unità di
misura, un valore e una precisione. Solo le misure possono
essere confrontate correttamente per poter fare delle valu-
tazioni. Dati puri non sono significativi. Il gateway aggiunge
a ogni misura anche l’informazione di quando è stata rilevata
affinché possa essere correlata con altre misure rilevate nello
stesso intervallo temporale.
L’invio dei dati alla piattaforma è un’importante fase che non
deve essere sottovalutata: oltre a non perdere dati, il gateway
deve garantire che non vengano manomessi (la sicurezza è
un problema da non sottovalutare mai). Infine, il percorso
contrario, da piattaforma a datagateway permette di inviare
parametri e comandi all’apparato produttivo. In questa fase
la sicurezza è ancora più importante per impedire la mano-
missione degli impianti.
Il secondo tipo di dispositivi che si possono adottare per
rilevare informazioni in ambito industriale sono i sensori
wireless. L’importanza di questi dispositivi risiede essen-
zialmente nella capacità di trasmettere a bassa potenza via
radio. In tal modo, pur alimentati a batteria possono operare
per anni. Sono ideali per applicazioni industriali dove l’im-
pianto produttivo può essere molto grande e non fornire
impianti di comunicazione facilmente accessibili.
Ad esempio il dispositivo UM2000A del produttore norve-
gese NAS è in grado di rilevare i segnali impulsivi emessi dai
meeter presenti su ogni macchinario produttivo.
Il secondo componente del servizio iNebula
Connect è la piattaforma
Compito della piattaforma è la raccolta dei dati e la messa
a disposizione in modalità standard affinché applicazioni
di alto livello possano utilizzarli. I vantaggi di questo ap-
proccio sono importantissimi: le applicazioni di alto livello
che visualizzano i dati raccolti sono del tutto indipendenti
dal sistema di produzione da cui sono stati raccolti; la sicu-
rezza dei dati è omogenea per tutta la linea di produzione;
i dispositivi di raccolta possono essere di diversa natura
per adattarsi alle differenti condizioni ambientali; le appli-
cazioni di alto livello possono fornire funzioni automatiche
per il controllo di produzione.
I vantaggi della soluzione
Senza spingersi nell’automazione
completa del processo produttivo,
proviamo a valutare gli effetti della
soluzione iNebula nel più semplice
processo di manutenzione. Che
l’impianto sia in un’unica sede o sia
costituito da molti dispositivi distri-
buiti (ad esempio impianti di riscalda-
mento) il processo di manutenzione
è supportato da molti strumenti soft-
ware. Anche nell’improbabile ipotesi
che lo strumento sia uno solo, lo sce-
nario tipico è il seguente: il software fornisce uno strumento
per inventariare gli impianti; permette di memorizzare gli
interventi effettuati; permette di programmare i prossimi
interventi. All’operatore spetta il compito di raccogliere ma-
nualmente tutte le informazioni su come/quanto l’impianto
ha lavorato tra un intervento programmato e un altro.
In molti casi questo è già un grande risultato di ottimizza-
zione, ma resta un grande difetto: la pianificazione degli in-
terventi avviene sempre in base a una valutazione statistica.
Ad esempio una caldaia viene controllata ogni anno, più o
meno nello stesso periodo, un forno ogni mese ecc.
Ma se l’impianto ha lavorato molto di più del previsto i para-
metri operativi potrebbero uscire dai limiti di lavoro ordinario
molto prima del previsto. Al contrario, se il sistema non ha
affatto lavorato come previsto, l’intervento potrebbe essere
posticipato. Si tratta in altre parole di un più elevato livello
di ottimizzazione del semplice processo di manutenzione
preventiva, che si può realizzare semplicemente grazie alla
raccolta di informazioni su come sta
funzionando l’impianto.
iNebula Connect può integrare i
software di gestione del processo di
manutenzione industriale in modo
semplice e poco invasivo installando
dei datagateway e/o dei sensori in
grado di rilevare il più ampio numero
di indicatori di funzionamento degli
impianti al fine di ottimizzare i pro-
cessi e migliorare la qualità della vita
delle persone in azienda e del pro-
dotto finale. Può inoltre inviare al-
larmi ai manutentori per evidenziare
situazioni eccezionali che richiedono
la loro attenzione. Pompe, filtri, val-
vole, componenti elettromeccanici, sensori, attuatori, ogni
tipologia di dispositivo utilizzato nel processo industriale
produce informazioni. Solo la sistematica raccolta di queste
informazioni permette di ottimizzare il processo di manuten-
zione, migliorando quindi la qualità finale del prodotto.
iNebula -
www.inebula.itIl datagateway 10-05 di Eurotech
Il dispositivo UM2000A
del produttore
norvegese NAS