Batterie, elettrificazione e intralogistica: una panoramica su cosa aspettarci in futuro
-
- Tweet
- Pin It
- Condividi per email
-
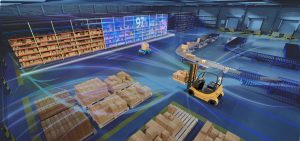
“Il collo di bottiglia oggi sono batterie e carica batterie, tutto il resto della tecnologia ha fatto passi da gigante e lo scopo all’interno dei magazzini è sempre e comunque quello di minimizzare i tempi di fermo di ogni singolo mezzo a prescindere da come sia alimentato”, spiega Davide Dal Pozzo Ceo di Elsa Solutions, società che opera nel mercato delle batterie con il proprio marchio Aliant Battery.
Storicamente l’intralogistica è legata al mondo dell’elettrificazione e delle batterie in particolare perché è sempre stato importante evitare la diffusione di gas combusti all’interno dei magazzini e delle aziende.
Inizialmente le batterie sono al piombo e svolgono il duplice compito di alimentare il carrello elettrico e di funzionare come contrappeso permettendo così il brandeggio e di spostare in quota merce pesante. Compito fino ad allora svolto a fianco del motore endotermico da semplici contrappesi, spesso in cemento.
Il passaggio alle più performanti batterie al litio (quelle dei cellulari, per dare l’idea) rappresenta un cambiamento importante in termini di performance, anche se, più leggere, tornano a rendere necessari i contrappesi. Un limite strutturale per nulla significativo, come vedremo, se messo a confronto con tutti i vantaggi che possono apportare al sistema.
È un tema importante quello delle batterie e dell’elettrificazione perché ha un valore dal punto di vista della politica industriale del Paese e tematica di interesse per Intralogistica Italia, la manifestazione fieristica di riferimento in Italia, in cui imprese, istituzioni e appassionati possono confrontarsi sulle soluzioni più funzionali.
La storia di questa tecnologia è ancora tutta da scrivere, come sostengono gli esperti che abbiamo intervistato, suggerendoci come, nei prossimi 24-36 mesi, assisteremo a grandi miglioramenti nelle prestazioni.
La spinta dell’automotive è forte, così come la necessità di differenziare il mix energetico nazionale; quindi, a cascata le novità spinte dai numeri dell’automotive ricadranno su tutti i settori laterali (come quello della logistica), ma molto incideranno anche le scelte politiche (con gli sgravi e/o gli incentivi) che si decideranno di percorrere.
Nell’impostare un confronto tra le diverse tipologie e le evoluzioni delle batterie ci aiuta Giorgio Forni, general manager di Battery Center Italia: “Come prima cosa è bene sottolineare che le tradizionali batterie al piombo richiedevano tempi di ricarica nell’ordine delle 8-12 ore, (un tempo che oggi risulta inimmaginabile, perché costringerebbe a raddoppiare o triplicare la flotta aziendale con costi che porterebbero ad uscire dal mercato ndr.). Inoltre, le batterie al piombo per carrelli elevatori erano, e in qualche parte sono ancora, al piombo acido e liberano idrogeno durante la ricarica che per non diventare esplosivo, in un ambiente chiuso, non può superare la concentrazione del 4%. Caratteristica che, evidentemente, ha sempre costretto a lasciare le stazioni di ricarica all’aperto, in zone ben areabili o dotate di aspiratori. Problema che non si presenta nel litio, ma neanche nelle batterie al piombo sigillate utilizzate tipicamente nei supermercati e in quelle situazioni che non presentano sale di ricarica ventilate o in aree esterne”.
Riassumendo le caratteristiche delle principali batterie, quelle al piombo hanno il vantaggio di non aver bisogno di contrappeso, necessitano di 8-12 ore di ricarica, emettono idrogeno e degradano più velocemente a seguito di numerose ricariche parziali. Data la necessità di avere un lungo periodo di ricarica non richiedono una infrastruttura particolare e quindi possono essere utilizzate quasi ovunque “facilmente” e senza sforare dai picchi di energia forniti dai “normali” gestori.
Ci chiarisce la questione Giorgio Forni: “Se una azienda ha 20 carrelli elevatori e vuole passare a un sistema di batterie al litio deve riadattare la sua infrastruttura. Le ricariche rapide, possibili con il litio, richiedono una densità energetica maggiore, abbiamo picchi di richieste di energia più violenti, che se riversate verso i fornitori tradizionali possono fare uscire l’azienda dalle normali fasce di consumo (superare certi picchi di assorbimento) e quindi arrivare a sovraccosti importanti”.
E qui subentra la questione del mix energetico perché, uno dei modi per sopperire a questi picchi è quello di avere una propria fonte rinnovabile di prossimità (ad esempio pannelli solari sul tetto) in grado di lavorare in questo senso, e/o vari “polmoni” (ad esempio intesi come modalità di accumulo, idrogeno) pronti a liberare energia nel momento del bisogno. Questa è certamente un’altra questione e non è detto che la tariffazione non possa cambiare o che, avendo una rete intelligente, non si possano organizzare i momenti di carica, per quanto brevi e diffusi in modo da non effettuarli in contemporanea.
Data l’esplosione dell’e-commerce che richiede velocità e annullamento di tempi di fermo non sarà questo il problema principale, ma sicuramente rappresenta, anche in prospettiva, una variabile da prendere in seria considerazione.
Se analizziamo la vita delle batterie possiamo dire che quelle al piombo tengono dai 1200-1500 cicli di ricarica, che diventano 450-800 nelle versioni sigillate (che non emettono idrogeno) mentre quelle al litio vanno dalle 1500 alle 15mila del litio titanato. Differenze importanti, che corrispondono a filosofie completamente diverse dal momento che le batterie al litio vivono sull’opportunity recharge e quindi sulla possibilità di essere ricaricate.
Parte proprio da qui il ragionamento di Davide Dal Pozzo di Elsa Solutions: “Negli ultimi 20 anni c’è stata una grandissima accelerazione nel miglioramento di tutti gli strumenti legati all’intralogistica, guidato dall’esplosione delle vendite online. E la parola d’ordine è flessibilità. Oggi la logistica deve essere distribuita (per poter consegnare ovunque a poche ore dall’emissione dell’ordine) e super efficiente, quindi grandi investimenti che, per definizione, devono essere massimizzati. Tutto questo si traduce nel dover avere un parco di muletti, carrelli elevatori, stoccatori e più in generale mezzi che movimentano materiali come Agv, Lgv, Amr, il più ridotto possibile, ma sempre in movimento. Non devono fermarsi mai, devono lavorare sempre, per questo il tempo di ricarica deve essere il più ridotto possibile” (e qui torniamo alla questione non secondaria dell’intensità energetica, ndr.).
In ogni caso sono tante le fonti che ci evidenziano come la ricerca sulle batterie sia in pieno sviluppo e come grandi investimenti si impegnino da relativamente pochi anni, quindi non possiamo che aspettarci novità. Continua Dal Pozzo: «la tecnologia al litio è in grande evoluzione e non è detto che da sola sia in grado di completare il panorama delle tecnologie che vedremo all’interno dei nostri magazzini, lo scenario è sempre in movimento. Il principio però è sempre lo stesso: se abbiamo strumenti super performanti, software, infrastrutture ad hoc e quindi tanti investimenti (ad esempio uno stoccatore a guida autonoma può arrivare a costare 300mila euro) se la mia opportunity charge dura 6 minuti all’ora vuol dire che ho un ecosistema che per il 10% del tempo sta fermo, sono queste due pause caffè all’ora quello su cui si sta lavorando…»
Da qui la considerazione definitiva sul confronto piombo – litio “le tecnologie al piombo sono state surclassate dal litio e hanno il limite dei tempi di ricarica, sensibilmente più lunghi rispetto al litio. Tenete conto che 60-90 secondi servono solo per predisporre la ricarica, mentre con il litio su 60 secondi di ricarica ho 60 secondi di ricarica (a prescindere da tutte le altre considerazioni tecniche ndr.).”
Le tecnologie corrono e così oggi (i mezzi più performanti) con uno stop di 5-6 minuti si riescono a recuperare 3-4 ore di lavoro abbassando il rapporto tra tempi di utilizzo e tempi di fermo. E continua “per risolvere il succitato problema legato ai picchi di richiesta di energia alla rete, a parte le reti intelligenti o i polmoni di accumulo, noi abbiamo studiato e già commercializzato un sistema ibrido, una centrale di cogenerazione idrogeno-batteria che utilizza idrogeno per produrre energia elettrica, che viene accumulata in batterie, che può essere messa in rete o utilizzata all’interno dell’intralogistica e attraverso una pompa di calore genera calore o freddo d’estate. Nel caso si riuscisse a lavorare con idrogeno verde si avrebbe un sistema a impatto ridottissimo e pronto a calmierare i picchi di richiesta”.
“In generale – conclude – sebbene si dica che tutta la tecnologia sia già in Cina e non ci siano possibilità di penetrare il mercato per le economie di scala, in verità ci sono ancora molte opportunità. L’elemento per lo storage viene sviluppato a “braccetto” tra chi progetta carrelli o veicoli, il tasso di specializzazione e la diversificazione dei singoli macchinari è così ampia che praticamente tutto è super targettizzato, anche la batteria; tutto è pensato per lavorare in quello specifico magazzino”. In ogni caso l’innovazione corre veloce, sappiamo cosa vedremo tra 24-36 mesi, ma successivamente, c’è davvero un altro mondo.
A questo proposito Alessandro Poletti, Managing Director di S.P.E. Elettronica Industriale, affronta il problema dal punto di vista di chi fa caricabatterie, l’altro “collo di bottiglia” del sistema.
“Con l’avvento delle batterie al litio il ruolo del caricabatterie nella sala di ricarica è sempre più importante, il litio garantisce performance in termini di durata del turno di lavoro e di efficienza di lavoro, però necessita di caricabatterie sempre più potenti che dialogano con le batterie attraverso sistemi di comunicazione CanBus”.
Tocca a loro affrontare il problema della densità energetica di cui sopra, infatti – continua Alessandro Poletti: “Questi vengono installati in strutture dove è possibile avere potenze disponibili limitate, per cui sempre più si sfrutta l’IoT, il cloud e l’analisi degli assorbimenti delle batterie, per far sì che i caricabatterie si dividano la potenza disponibile nel momento in cui serve senza sforare i picchi di assorbimento e senza costringere l’azienda a stipulare contratti energetici con potenze installate molto alte”.
Sistemi sempre più intelligenti che sempre di più hanno a che fare con dati e software, da commodity a elementi periferici, ma sempre più centrali nella catena di valore.
“Nel nostro ambito l’innovazione più importante è quella dei caricabatterie wireless che eliminano l’operatore e prevedono l’infrastrutturazione di una zona di ricarica, a cui i mezzi possono accedere autonomamente. È un sistema ideale se si pensa alla filosofia di un “biberonaggio” continuo, senza attriti e liberi dallo stress della connessione meccanica”.
Anche qui l’evoluzione è continua, se si pensa che le prime tecnologie disperdevano il 30-40% dell’energia e oggi siamo a un’efficienza, utilizzando il gallio, del 93-94%.
Prestazioni tanto differenti, spesso ignorate dai più, che non colgono l’importanza delle stazioni di ricarica, le quali a loro volta devono rispondere alle esigenze di riduzione dello spazio da impegnare e alla flessibilità.
“In ogni caso – chiude Poletti – l’evoluzione dei caricabatterie fa sì che anche gli accumulatori tradizionali vedano le loro performance migliorate, sia in termini di prestazioni, sia in numero di cicli e quindi di tempo di vita della batteria. Per questo prima di cambiare il mezzo è meglio cambiare lo strumento di ricarica. Per fare un semplice esempio, pur avendo solo 2-3 carrelli elevatori, se passo da uno strumento che ha una efficienza del 50-60% a uno che ne ha il 90%, ho un risparmio di qualche migliaio di Euro”.
Contenuti correlati
-
Economia circolare, Siemens e Osai GreenTech al recupero dei metalli preziosi dai RAEE
Nell’economia lineare l’estrazione, la lavorazione e lo smaltimento dei metalli preziosi comportano un consumo smisurato di risorse naturali, generano rifiuti tossici e hanno un impatto negativo sulle comunità locali. Il recupero di questi materiali dai rifiuti elettronici...
-
Hewlett Packard e Danfoss insieme per ridurre il consumo energetico nei data center
Hewlett Packard Enterprise e Danfoss collaborano per la fornitura di HPE IT Sustainability Services – Data Center Heat Recovery, un modulo di recupero del calore pronto all’uso che contribuisce a gestire e valorizzare il calore in eccesso...
-
AI in simulazione e HPC con Altair al Farnborough Airshow 2024
Altair porta in mostra le ultime innovazioni nel campo della simulazione ingegneristica, dell’intelligenza artificiale (AI) e del calcolo ad alte prestazioni (HPC) al Farnborough International Airshow 2024, in programma dal 22 al 26 luglio presso il Farnborough...
-
Efficienza energetica e decarbonizzazione al centro della filiera dell’alluminio
Dopo un periodo che ha visto il comparto affrontare diverse sfide, l’industria dell’alluminio sta mostrando segnali incoraggianti di ripresa. I dati del 2024 rivelano, infatti, un quadro positivo: l’indice degli ordini dei laminati ha registrato un incremento...
-
Più sostenibilità con il monitoraggio dell’energia
I software di Schneider Electric permettono di analizzare e ridurre i consumi, migliorare l’efficienza e la continuità operativa di un processo altamente energivoro. I dati accurati raccolti con questi software aiutano Dife nella redazione del bilancio annuale...
-
Intervista a Massimiliano Rottoli, RS Italia
RS Italia è un fornitore globale omnicanale di prodotti e soluzioni per progettisti, costruttori, manutentori e riparatori. Distribuisce più di 750.000 prodotti di oltre 2.500 fornitori diversi. Automazione Oggi ha intervistato Massimiliano Rottoli, managing director di RS...
-
Schneider Electric lancia la III edizione dei Sustainability Impact Awards
Schneider Electric ha aperto le candidature per la terza edizione del premio Schneider Electric Sustainability Impact Award. Questa iniziativa, inaugurata nel 2022, valorizza il contributo che l’ecosistema di clienti, partner e fornitori di Schneider Electric offre alla...
-
Fare ‘Sustainable Manufacturing’ per produrre in Europa
La sostenibilità è sempre più al centro di qualsiasi iniziativa di innovazione della produzione. Occorre tuttavia non farsi disorientare da chi parla di Industria 5.0 come di ‘nuova rivoluzione’ e concentrarsi piuttosto su una corretta implementazione del...
-
Soluzioni di automazione Bosch Rexroth per la produzione di batterie per EV
La domanda di soluzioni per l’accumulo di energia è in questa fase storica più che mai elevata, spinta dall’espandersi delle vendite di auto elettriche, dal proliferare di dispositivi elettronici e dalla diffusione di nuove tecnologie per l’edilizia....
-
Rollon China inaugura un nuovo stabilimento all’avanguardia a Suzhou
1° luglio 2024: Rollon, fornitore di soluzioni per il movimento lineare, annuncia l’inaugurazione del nuovo stabilimento a Suzhou, in Cina: questa nuova struttura segna un significativo passo avanti nella strategia di localizzazione e nell’espansione strategica di Rollon e...
Scopri le novità scelte per te x
-
Economia circolare, Siemens e Osai GreenTech al recupero dei metalli preziosi dai RAEE
Nell’economia lineare l’estrazione, la lavorazione e lo smaltimento dei metalli preziosi comportano un consumo smisurato di risorse...
-
Hewlett Packard e Danfoss insieme per ridurre il consumo energetico nei data center
Hewlett Packard Enterprise e Danfoss collaborano per la fornitura di HPE IT Sustainability Services – Data Center...
Notizie Tutti ▶
-
Economia circolare, Siemens e Osai GreenTech al recupero dei metalli preziosi dai RAEE
Nell’economia lineare l’estrazione, la lavorazione e lo smaltimento dei metalli preziosi comportano un consumo...
-
1° ottobre, appuntamento con la II edizione dell’IO-Link Day
Sulla scia del successo della prima edizione, torna l’evento di Consorzio PI Italia dedicato...
-
Hewlett Packard e Danfoss insieme per ridurre il consumo energetico nei data center
Hewlett Packard Enterprise e Danfoss collaborano per la fornitura di HPE IT Sustainability Services...
Prodotti Tutti ▶
-
Sensori di corrente a rilevamento magnetico di Allegro per industria, automotive ed energie rinnovabili
Allegro MicroSystems ha sviluppato i sensori di corrente ad alta potenza ACS37220 e ACS37041,...
-
InnoTrans 2024: Moxa presenta le soluzioni di comunicazione ed elaborazione dati con protezione
Moxa, fornitore di soluzioni di comunicazione basate su IP, si presenterà a InnoTrans 2024...
-
Refrigeratori di acqua di processo ecologici di Parker a basso GWP
Parker Hannifin ha sviluppato Hyperchill Plus-E, un nuovo refrigeratore ecologico per processi industriali utilizzato...