Aumento dell’utilizzo e del tempo di disponibilità per Barrett Steel grazie alla trasformazione digitale
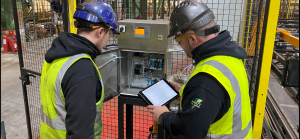
CHG Electrical trasforma completamente con Rockwell Automation le operazioni degli stockholder dell’acciaio con il CMMS Fiix e il software ThingWorx Industrial Internet of Things. “Tutti i dati erano già disponibili, non li raccoglievamo… o non li usavamo”, spiega Paul Burke, Head of Engineering di Barrett Steel , il più grande stockholder indipendente del Regno Unito.
Una premessa relativamente semplice che da allora si è evoluta nella forza trainante di una straordinaria trasformazione digitale, sostenuta dal pacchetto SCP (prodotti connessi intelligenti) basato su SaaS ThingWorx di PTC e dal Computerized Maintenance Management System (CMMS) Fiix di Rockwell Automation.
Questa evoluzione ha portato a grandi risparmi in termini di budget, tempo macchina improduttivo, ore dei dipendenti, trasporto e consumo energetico, per non parlare di un regime di manutenzione proattiva completamente revisionato… E c’è ancora molto da realizzare.
Quando ha assunto il ruolo di Head of Engineering in tutti i siti di Barrett Steel, Burke ha applicato una mentalità basata sulla sua esperienza nella produzione e sull’identificazione di efficienze operative significative in tutti gli aspetti dell’azienda. Ma queste efficienze sarebbero diventate evidenti solo avendo informazioni molto più chiare e approfondite sulle varie operazioni, tra cui uffici, gru, carico, taglio, logistica e manutenzione.
“Volevo quanti più dati operativi possibili, tra cui consumo di energia, tempo di funzionamento, tempi di fermo, riparazioni, sedi dei veicoli e produttività, solo per citarne alcuni”, spiega Burke. “Avevo bisogno di dati operativi contestualizzati su cui basare le mie decisioni e aiutare i responsabili delle operazioni a prendere le loro decisioni, non solo in relazione a una macchina e a un sito, ma in tutta l’azienda”
Concentrandosi inizialmente sulla capacità delle macchine e sul tempo di consegna degli ordini, il primo sistema cartaceo di Burke ha subito una rapida evoluzione. Con l’aiuto di CHG Electrical , un fornitore di fiducia di Barrett Steel e membro della PartnerNetwork di Rockwell Automation come integratore di sistemi riconosciuto, il nuovo approccio si è concretizzato in una soluzione elettronica per la raccolta dei dati, supportata da controllori a logica programmabile (PLC) e dal software Rockwell Automation che forniscono un’interfaccia fondamentale per le metriche a livello di macchina.
Peter Clarke, CEO di CHG Electrical, spiega: “Paul stava cercando di identificare i motivi dei tempi di fermo, come la manutenzione, la mancanza di scorte o la disponibilità del personale. Pertanto, abbiamo eseguito una prova su una macchina in un sito e quindi estrapolato questi dati in tutti i siti con macchine simili. Ci siamo subito resi conto che esisteva una motivazione aziendale molto solida per un grande progetto di integrazione che comprendeva 52 macchine in 10 siti”.
In questa fase, CHG e Barrett Steel hanno concordato che un software dedicato sarebbe stato un approccio migliore per soddisfare tutte le diverse fonti di dati, facilitare l’espansione prevista e garantire l’eventuale modularità su più siti. Questa decisione ha portato all’implementazione della piattaforma ThingWorx e del CMMS Fiix.
Grazie a questi strumenti e a una capacità più semplificata di raccogliere e analizzare i dati, Barrett Steel e CHG hanno iniziato a identificare altre operazioni potenzialmente ricche di dati che potevano essere analizzate e migliorate.
Ad oggi, i risultati sono stati davvero impressionanti. “Abbiamo eseguito una prova su una macchina in un sito, il che ha evidenziato che un miglioramento dell’1% nell’utilizzo avrebbe comportato 250.000 sterline di reddito aggiuntivo”, afferma Burke. “Anche un miglioramento conservativo del 5% equivale a più di 1 milione di sterline di ricavi aggiuntivi.
Abbiamo quindi estrapolato i risultati in tutti i siti con macchine simili. “Abbiamo anche esaminato i tempi di fermo non pianificati e abbiamo scoperto che quando abbiamo utilizzato dati standard del settore, anche se piuttosto conservativi, 5 milioni di sterline di tempi di fermo potevano essere migliorati semplicemente gestendo meglio i 40 tecnici della cura degli asset. Anche un miglioramento del 10% equivale a 500.000 sterline. È stata proprio questa consapevolezza a determinare l’implementazione di Fiix.
“Il 90% del lavoro di manutenzione del nostro team di gru è ora proattivo”, spiega. “In effetti, utilizzando l’approccio rudimentale originale, il ritorno sull’investimento in un sito con otto macchine sarebbe stato di soli sei mesi; con l’implementazione di Fiix in tutti i siti, possiamo aspettarci un ritorno sull’investimento altrettanto impressionante.
“Utilizzando ThingWorx per acquisire e raccogliere i dati, abbiamo anche identificato una capacità in eccesso di macchine in altri siti, per un valore di 300.000 sterline. Se questo si traduce in spese di capitale per nuove gru, caricatori e carrelli elevatori, giustificheremo l’investimento in ThingWorx per quattro anni, con un risparmio di un solo anno”.
E non è solo il lavoro pesante che ha beneficiato di questo nuovo paradigma basato sui dati. Burke ha anche identificato e misurato altre discipline nell’ambito delle operazioni aziendali.
“Grazie a ThingWorx che è basato sul cloud e che offre API aperte”, continua Clarke, “possiamo estrarre altre fonti di dati eterogenee che in precedenza non venivano esaminate da Barrett Steel e contestualizzarle con altri dati operativi. La logistica e il consumo energetico sono una parte importante di tutto questo.
“Dal punto di vista dei trasporti, guardiamo ai veicoli in termini di consumo di carburante, chilometri percorsi e peso dell’acciaio che viene spostato. Grazie a questo, possiamo usare i veicoli più adatti al compito. Utilizziamo ThingWorx anche per esaminare l’uso di elettricità misurando il consumo in base ai diversi turni. Abbiamo scoperto che più di 1,2 milioni di sterline o il 40% del consumo elettrico si verificava durante i turni a riposo, a causa della presenza di luci o di apparecchiature lasciate in funzione, quindi abbiamo immediatamente messo in atto un piano di riduzione delle emissioni di CO2 che avrebbe risolto le perdite d’aria, spento le macchine non necessarie, risolto l’uso improprio dell’illuminazione con sensori di lux e presenza e migliorato l’infrastruttura per la generazione di energia solare esistente. Tutti questi risparmi si riflettono direttamente sui profitti.”
“Al momento non usiamo una vera e propria OEE”, continua Burke. “Al momento stiamo solo esaminando l’utilizzo e la disponibilità, ma in futuro includeremo anche le prestazioni. Anche la qualità non rappresenta un problema, in quanto i tassi di scarto sono così ridotti che il vantaggio è davvero minimo per noi. Sicuramente vedremo un aumento della produttività, ma al momento non si tratta di una metrica chiave: attualmente, siamo in una fase di individuazione dei problemi.
“Detto ciò, in un sito di Bradford, ottenendo oltre l’80% di OEE/utilizzo delle macchine, abbiamo osservato un incremento dei prodotti sui veicoli e in uscita, un maggior numero di conducenti in orario, e una riduzione marcata degli straordinari dei conducenti e del lavoro nei weekend, grazie alla migliore pianificazione del traffico e delle ore di punta.
“Inoltre, non abbiamo perso di vista quanto siano importanti le persone nel quadro complessivo. È fondamentale che le persone operino con e sui dati. Anche se è possibile raccogliere e monitorare i dati, senza un’azione mirata e decisioni operative che producano risultati reali, la motivazione a utilizzarli si riduce. È importante usarli ed essere motivati a usarli.
“All’inizio, c’era la percezione che stessimo monitorando gli operatori piuttosto che le macchine. Ma dopo aver dimostrato il nostro focus sulle macchine e aver presentato i risultati ottenuti, l’atteggiamento è cambiato notevolmente, in modo molto più evidente rispetto alle linee non monitorate. Non solo l’atteggiamento è diverso, ma i livelli di produttività sulle linee monitorate sono migliorati notevolmente. Guardando al progetto nel suo insieme, non abbiamo ancora completato tutto, ma la meta si avvicina sempre di più.”
Burke riserva l’espressione più convincente per la fine; ed è quella che ha usato davanti al suo team di management, dopo aver presentato la proposta aziendale per la trasformazione digitale. Ha semplicemente detto: “Sta a voi decidere se possiamo permetterci di farlo, ma io sono convinto che non possiamo permetterci di non farlo!”
Contenuti correlati
-
Probiotical sceglie Impresoft per implementare la trasformazione digitale
Probiotical S.p.A., leader italiano nella produzione di probiotici, ha scelto Syscons Industries, parte del Gruppo Impresoft, e gli strumenti di Rockwell Automation al fine di accelerare la propria trasformazione digitale. Per rispondere alla rapida e crescente richiesta...
-
Windchill di PTC al centro della trasformazione digitale del Gruppo Carraro
PTC è stato selezionato quale fornitore strategico dal Gruppo Carraro, che ha scelto Windchill quale piattaforma PLM (Product Lifecycle Management) di ultima generazione per gestire il ciclo di vita dei suoi prodotti in un’ottica di integrazione della...
-
Rockwell Automation e Microsoft: una visione condivisa per accelerare la trasformazione industriale
Rockwell Automation e Microsoft espandono la loro collaborazione strategica per trasformare il panorama industriale. Insieme, le due aziende offriranno ai clienti del settore manifatturiero soluzioni avanzate basate su cloud e AI, che forniscono potenti insight sui dati, semplificano...
-
Partnership tra FasThink e DM Management & Consulting-TXT
Le due realtà italiane FasThink, system integrator specializzato in tecnologie e soluzioni innovative per il miglioramento dei processi nella logistica e nel manufacturing e DM Management & Consulting, società del Gruppo TXT e-solution, attiva nello sviluppo di...
-
Rockwell Automation dà vita alle operazioni autonome utilizzando Nvidia Omniverse
Rockwell Automation ha annunciato l’integrazione delle interfacce di programmazione delle applicazioni (API) di Nvidia Omniverse nel proprio software Digital Twin Emulate3D per ottimizzare le operazioni di fabbrica tramite l’intelligenza artificiale e la tecnologia di simulazione fisica. I digital twin ottimizzano...
-
Rockwell Automation collabora con Taurob per offrire soluzioni complete di automazione robotica
Rockwell Automation ha siglato un accordo con Taurob (Dietsmann Group) per fornire una soluzione robotica olistica, mirata a supportare le organizzazioni industriali nel loro percorso verso operazioni autonome all’interno degli stabilimenti. Taurob è specializzata nella progettazione e...
-
Trasformazione digitale del manifatturiero, la suite di Rockwell Automation per i lavoratori connessi
Rockwell Automation ha rilasciato la soluzione Connected Worker di Plex. Queste funzionalità all’avanguardia nel settore sono state sviluppate per aiutare gli utenti a migliorare la produttività, la qualità e la sicurezza nell’area della produzione. Le aziende manifatturiere...
-
Gustavo Zecharies neopresidente di Rockwell Automation per la Regione Emea
Rockwell Automation ha annunciato che Gustavo Zecharies è stato nominato presidente della regione Europa, Medio Oriente e Africa (Emea), con effetto immediato. In qualità di presidente, Zecharies riporterà a Scott Genereux, SVP e Chief Revenue Officer, e succede...
-
Università, impresa e ricerca fanno rete con il Digital Transformation and Technology Transfer Hub di Unipa
Un ecosistema aperto per promuovere e stimolare i processi innovativi di trasformazione delle imprese e, contemporaneamente, offrire opportunità di crescita e di successo ai tanti talenti e alle diverse professionalità che si formano all’interno dell’Ateneo in uno...
-
Creare le soluzioni di domani
In linea con le ultime tendenze del mercato, Mitsubishi Electric sta integrando la già ampia offerta con nuove soluzioni software basate sull’utilizzo dell’intelligenza artificiale, allo scopo di supportare le aziende nel loro processo di trasformazione digitale In...