I robot ABB per la produzione dei motori Baldor
Invece di delocalizzare la produzione per risparmiare sui costi, Baldor ha migliorato il livello di produttività dei propri stabilimenti negli Stati Uniti, adottando procedure automatizzate e metodi di produzione più efficienti. Il ruolo dei robot ABB.
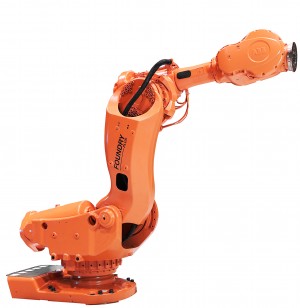
Nel 1920, Edwin Ballman ed Emil Doerr immaginavano che, in un mondo futuro, quasi tutti gli aspetti della vita quotidiana sarebbero dipesi dai motori elettrici e che, in un mondo così, le fonti energetiche sarebbero state limitate e l’efficienza energetica sarebbe diventata fondamentale. Insieme, fondarono Baldor Electric Company, con lo scopo di concentrarsi su queste esigenze di affidabilità e di efficienza. Oggi questa previsione, in un mondo che dipende sempre più dai motori elettrici, è più che mai valida. Baldor propone soluzioni per ogni esigenza, dai piccoli motori da 1/50° hp di potenza fino a quelli più grandi con una potenza da 15.000 hp e oltre. Con il passare degli anni, la società si è sviluppata fino a diventare uno dei più noti marchi al mondo di apparecchiature elettriche e il più grande produttore di motori e di soluzioni per la trasmissione di potenza meccanica del Nord America.
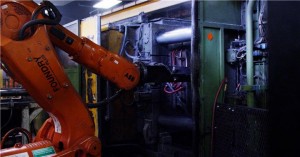
Un robot industriale ABB estrae componenti da un macchinario per pressofusione nello stabilimento Baldor di Fort Smith
«Ballman era un ingegnere elettrico e Doerr un operaio meccanico; il loro intento era quello di costruire un motore migliore», afferma Ryan Fitts, assistente responsabile dello stabilimento Baldor “210 Motor Facility”. «Con la parola “migliore” intendevano un motore più efficiente ed è lo stesso obiettivo che perseguiamo ancora oggi». Negli anni, l’azienda si è trasformata da una piccola officina a una realtà produttiva con più di 7.000 dipendenti in Nord America e recentemente è entrata a far parte del gruppo ABB. Ora le due organizzazioni operano insieme ed entrambe hanno ampliato la propria presenza sul mercato globale. Insieme, ABB e Baldor offrono un’ampia gamma di motori industriali, convertitori di frequenza e sistemi di trasmissione meccanica destinati soprattutto ai costruttori di macchine (OEM) e ai distributori. «Siamo un’azienda orientata al cliente», afferma Fitts «e vogliamo realizzare i prodotti che i nostri clienti desiderano acquistare e non i prodotti che desideriamo vendere».
Investimenti congiunti per garantire la permanenza della produzione negli Usa e assicurare la sicurezza del personale
Dal momento che la maggior parte dei clienti di Baldor si trovano in Nord America, la strategia adottata è sempre stata quella di investire su stabilimenti produttivi che fossero il più vicino possibile ai clienti, in modo da poter garantire consegne rapide e assistenza a livello locale. Invece di delocalizzare la produzione per risparmiare sui costi, Baldor ha volutamente migliorato il livello di produttività dei propri stabilimenti negli Usa, adottando una combinazione di procedure automatizzate e introducendo metodi di produzione più efficienti. Un altro importante beneficio di questa scelta di automazione è stato la creazione di un ambiente di lavoro sicuro per i dipendenti, come confermato dal cartello che compare nello stabilimento, nel quale si dichiara che, durante i processi di produzione, si è lavorato per ben 8.000.000 di ore-uomo senza incidenti significativi.
Video
Da molti anni, l’utilizzo di robot è un elemento chiave della strategia per mantenere la produzione vicina ai clienti. Nella sede principale di Fort Smith, in Arkansas, Baldor ha iniziato a usare i robot ABB nel 2000, nello stabilimento Southwestern Die Casting per la produzione di tutti i componenti di alluminio pressofuso dei motori Baldor. I processi di lavorazione di una fonderia come questa sono “sporchi” e pericolosi e quindi particolarmente adatti all’automazione robotizzata. Con il passare del tempo, Southwestern Die è passata da un solo robot a una serie di 9 robot, tra cui un ABB IRB 6640, IRB 6600, IRB 4600 e IRB 4400. «Uno di questi 9 robot è ancora quello originale della prima installazione», afferma Jed Reinhard, direttore tecnico e della manutenzione di Southwestern Die. «Gli altri sono in attività da molti anni – da cinque a sette – a seconda della difficoltà delle applicazioni alle quali sono destinati».
«I robot ci hanno consentito di far funzionare un numero sempre maggiore di stampi multipli più velocemente», afferma Mike Gipson, supervisore di produzione di Baldor Die Casting. «Sono estremamente affidabili e non fanno pause. Inoltre, gli stampi multipli prodotti nelle nostre celle robotizzate possono essere anche relativamente pesanti e stancare molto gli operatori umani che devono movimentarli. I robot non conoscono la fatica e non rischiano alcun tipo di lesione durante queste attività». Oltre a questo tipo di lesioni da stress ripetitivo, comuni per tutti i lavoratori che spostano abitualmente carichi pesanti, in fonderia i lavoratori sono anche esposti ad altri tipi di rischi. «La protezione ABB Foundry Plus di questi robot garantisce la continuità produttiva anche in condizioni critiche».
«In questo stabilimento siamo soggetti a condizioni atmosferiche dure che contribuiscono a determinare una situazione ambientale abbastanza critica», afferma Gipson. «La temperatura è molto elevata e nell’aria sono presenti polveri di alluminio e particelle di lubrificanti in sospensione. Per un essere umano può essere un problema, ma la protezione ABB Foundry Plus di questi robot ne garantisce l’operatività anche in condizioni critiche. In linea generale, dopo aver installato e programmato un robot, non c’è molto altro da fare, se non metterlo in funzione. Possiamo contare su vari anni di operatività di un robot prima che si presenti un qualsiasi tipo di problema dovuto a logorio e usura».
«In questo ambiente, sporco e a temperatura elevata, con particelle di lubrificante in sospensione nell’aria, la possibilità di usare nelle celle un robot invece di personale umano è una condizione per noi ottimale», aggiunge Reinhard. «Gli operatori possono gestire più macchine e non devono movimentare materiale pesante. Siamo particolarmente soddisfatti delle prestazioni dei robot; il loro uptime e la loro lunga vita operativa si sono realmente dimostrati una risorsa per tutti noi».
La pressofusione dell’alluminio è un processo complesso che si svolge in condizioni di pressione e di temperatura davvero eccezionali. Quando il pezzo si raffredda, si ritrae in modo evidente e, alcune volte, quello che fa la differenza fra un rilascio corretto o un grippaggio è proprio la possibilità di movimento millimetrico del robot. «Con la nuova programmazione e le funzioni più recenti applicate alle nostre celle robotizzate siamo in grado di apportare modifiche immediate», aggiunge Gipson. «Non siamo costretti ad arrestare la cella dopo il cambio degli stampi per regolare il processo e abbiamo la possibilità di risolvere qualsiasi problema di lieve entità in modo facile e veloce. La manutenzione dei robot è facile, grazie anche alla semplicità di intercambiabilità dei componenti».
Vicino all’impianto Southwestern Die di Fort Smith, troviamo il nuovo impianto di bobinatura Baldor che si sta espandendo adottando robot che giocheranno un ruolo chiave nella bobinatura dei fili di rame nei motori. Questo impianto, denominato “210 Facility” rappresenta la filosofia di Baldor per quanto riguarda il futuro della produzione di motori. A partire dalla movimentazione dei materiali, che non dovranno più essere sollevati da personale umano, fino ad arrivare all’incredibile flessibilità dell’impianto stesso (in grado di produrre migliaia di diverse varianti di motori su una sola linea), le pareti bianche e pulite di “210 Facility” rappresentano un chiaro contrasto con l’ambiente “sporco” di una comune fonderia.
«Una delle strategie adottate da sempre da Baldor è stata quella di rimanere negli Stati Uniti», afferma Steve Morse, responsabile tecnico di Baldor, «e per farlo ha dovuto mantenere i costi al livello più basso possibile. A mano a mano che aumenta la complessità e la personalizzazione dell’offerta delle nostre soluzioni, dobbiamo anche prevedere, per la produzione dei nostri prodotti, l’adozione di processi aggiuntivi e il solo modo per ridurre i costi correlati è l’adozione della robotica e dell’automazione».
Nell’impianto “210 Facility” i robot vengono utilizzati nella fase, difficile e complessa, dell’avvolgimento delle bobine di rame. Il numero e la lunghezza delle bobine sono diversi in ogni fase di produzione e per ogni cliente; in questo processo, i robot offrono un alto livello di flessibilità. Inoltre, le parti dei motori sono particolarmente pesanti e l’utilizzo dei robot per la loro movimentazione da una stazione di bobinatura all’altra evita che il personale venga esposto a lavorazioni faticose e a possibili incidenti. Questa filosofia di protezione contro gli incidenti viene adottata in tutto l’impianto “210 Facility” sotto forma di navette progettate ergonomicamente e di sollevatori aerei adeguatamente posizionati.
Attualmente, presso il “210 Facility” sono in funzione due celle di bobinatura con un robot ABB IRB 7600 in ogni cella, ma il progetto prevede che per l’anno prossimo, al termine del processo di espansione, le celle saliranno a quattro, così come previsto dai piani di Fitts. «Per ora siamo ancora allo stadio di sviluppo», aggiunge. «Alla conclusione dell’operazione, e quando saremo a pieno regime, questo impianto sarà un modello al quale in futuro dovranno fare riferimento tutti gli stabilimenti Baldor. Si tratta di un processo particolarmente efficiente che non sarebbe stato possibile senza l’automazione e la robotica. Il contributo di ABB a questo progetto è stato davvero straordinario».
Contenuti correlati
-
Robot Scara e sistemi di visione con Macco, Omron e Werfen nei laboratori clinici
Per la fornitura di reagenti destinati ai laboratori di farmaco-tossicologia, Werfen ha implementato una nuova macchina automatica realizzata da Macco in collaborazione con Omron e Marini Pandolfi che utilizza robot Scara e sistemi di visione avanzati per...
-
Un customer experience center per vedere all’opera i sensori di forza dei robot
Bota Systems, azienda che produce sensori di forza/coppia multiasse, ha aperto il suo Customer Experience Center presso il Connect Manufacturing Innovation Hub di Heidenhain a Fremont, in California. Il centro ospiterà l’intero portfolio di sensori di forza/coppia di...
-
Celle di carico avanzate per sistemi robotici
Le celle di carico di Picotronik sono progettate per portare precisione e sicurezza nelle operazioni industriali complesse e offrire soluzioni avanzate per robot e cobot. Resistenti e personalizzabili, aiutano a migliorare l’efficienza e ottimizzare la manutenzione predittiva....
-
Il sensore di forza ultra preciso di Bota per i cobot UR con payload elevati
SensOne T80 di Bota Systems è un sensore specifico per i robot collaborativi con carico utile elevato provvisto di flange ISO su entrambi i lati, caratteristica questa che ne semplifica l’integrazione e che assicura una precisione eccellente...
-
Soluzioni di automazione su misura Keba in SPS 2024
Keba Industrial Automation sarà presente SPS 2024 di Norimberga (Pad. 7, Stand 470) dove punterà su soluzioni integrate, digitalizzazione e intelligenza artificiale. La versatilità del portfolio prodotti si riflette in Kemro X, la piattaforma aperta e flessibile...
-
Automazione, educazione e stampa 3D con DigiKey alla Maker Fair Rome
DigiKey, un distributore commerciale attivo a livello mondiale che offre una vasta selezione di componenti tecnici e prodotti di automazione a magazzino per la spedizione immediata, sarà presente alla Maker Fair Rome, dal 25 al 27 ottobre...
-
Oltre 750 espositori (+8,5%) e 35.000 visitatori, i numeri della 34.BI-MU
Si è chiusa sabato 12 ottobre, 34.BI-MU, biennale internazionale dedicata all’industria costruttrice di macchine utensili, robot, automazione, digital e additive manufacturing e subfornitura, in scena a fieramilano Rho da mercoledì 9 ottobre. Organizzata da EFIM-Ente Fiere Italiane...
-
B&R a SPS Norimberga 2024: soluzioni aperte per sbloccare nuovi livelli di produttività
A SPS Norimberga 2024, in programma dal 12 al 14 novembre a Norimberga, in Germania, i visitatori dello stand 206, all’interno del padiglione 7, potranno sperimentare come B&R stia aiutando i costruttori di macchine, gli integratori e gli...
-
Tanti premi alla 34.BI-MU
In occasione di 34.BI-MU, la biennale internazionale dedicata all’industria costruttrice di macchine utensili a asportazione, deformazione e additive, robot, digital manufacturing e automazione, tecnologie abilitanti e subfornitura, sono stati consegnati numerosi premi. In particolare la fiera, promossa da Ucimu-Sistemi...
-
Soluzioni per Machinery & Automation Hilti dalla 34.BI-MU
Hilti Italia, ha presentato in occasione della 34.BI-MU in Fieramilano Rho, la biennale dedicata all’industria costruttrice di macchine, robot, automazione, digital e additive manufacturing, le sue soluzioni tecnologiche per il settore Machinery & Automation. Tra le novità di...