Oltre il trasporto: l’evoluzione di XTS con la tecnologia NCT

Dalla rivista:
Automazione Oggi
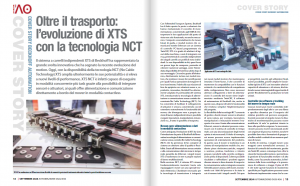
Il sistema a carrelli indipendenti XTS di Beckhoff ha rappresentato la grande svolta innovativa che ha segnato la recente evoluzione del motion. Oggi, con la disponibilità della tecnologia NCT (No Cable Technology) XTS amplia ulteriormente le sue potenzialità e si eleva a nuovi livelli di performance. XTS NCT è infatti capace di eseguire in modalità concorrente più task grazie alla possibilità di integrare sensori e attuatori, ai quali offre alimentazione e comunicazione direttamente a bordo del mover in modalità contactless
Con l’eXtended Transport System, Beckhoff ha di fatto aperto le porte a soluzioni che hanno rivoluzionato il concetto di movimentazione, consentendo agli OEM di reinterpretare le loro applicazioni dal punto di vista non solo funzionale, ma anche meccanico. Composto essenzialmente da mover, binari di guida, e moduli motore che comunicano tramite Ethercat con un sistema di controllo PC-based programmato via TwinCAT, XTS è in grado di adattarsi al layout della macchina, e anzi di integrarsi con essa, permettendo il controllo indipendente dei singoli carrelli con profili di moto individuali. La sua disponibilità in kit, quasi fosse un grosso lego da comporre, permette di ottenere numerosi vantaggi, come l’immediata disponibilità del sistema subito dopo il suo montaggio. Ciò anche grazie all’elettronica, direttamente inclusa nei moduli motore, che rendono i mover dei carrelli passivi per i quali l’unica operazione da eseguire è il loro inserimento. Fedele alla sua missione di fare da apripista con soluzioni nuove e, soprattutto, innovative, Beckhoff ha ulteriormente ampliato le potenzialità del sistema XTS, introducendo la tecnologia di alimentazione e comunicazione senza contatto denominata No Cable Technology (NCT). Ciò ha consentito di facilitare il collegamento di attuatori e sensori, consentendo così di estendere notevolmente le funzionalità dei mover, che divengono vere e proprie stazioni di lavoro indipendenti dove è possibile eseguire lavorazioni, manipolazioni, misurazioni ecc., il tutto in parallelo al trasporto.
Nessun cavo: alimentazione e dati in modalità contactless
Come anticipato, l’evoluzione di XTS ha visto l’introduzione da parte di Beckhoff dell’innovativa tecnologia di alimentazione e comunicazione senza contatto No Cable Technology (NCT) che ha permesso di far compiere al sistema un ulteriore salto di qualità e flessibilità. Grazie all’alimentazione senza contatto e alla comunicazione dati sincrona in tempo reale garantita da Ethercat, i singoli mover XTS si trasformano in vere e proprie stazioni di lavoro multifunzionali. Nella versione NCT, il sistema XTS rimane fondamentalmente invariato: basta solo equipaggiare i mover con uno speciale modulo elettronico. L’hardware necessario per la tecnologia di trasmissione è integrato nei nuovi moduli motore che mantengono invariato il form-factor, il che consente di mantenere la compatibilità con le funzioni esistenti e le caratteristiche di compattezza della configurazione. Non sono necessari ulteriori collegamenti o linee di alimentazione: il controllo del mover viene implementato mediante TwinCAT, il software di automazione di Beckhoff che, anche in questo caso, dispone di tutte le funzionalità che rendono semplice l’implementazione del progetto. La flessibilità della tecnologia NCT consente di gestire a bordo mover sensori e attuatori di varia natura, per esempio, lavorazioni, manipolazioni o misurazioni mentre il trasporto è in corso. Grazie alla comunicazione Ethercat, sensori e attuatori possono comunicare con il sistema di controllo in tempo reale, con una sincronizzazione degli eventi spinta ai microsecondi. A titolo di esempio, sui mover possono essere implementate operazioni di orientamento del prodotto. In questo caso il mover si trasforma in un sistema di manipolazione mobile che, mediante pinze elettromeccaniche, magneti o ventose, preleva, trasferisce e intanto prepara i prodotti nella corretta configurazione prima di depositarli. È altresì possibile riscaldare o raffreddare i prodotti oppure rilevare misure in linea durante il trasporto: la comunicazione veloce integrata consente l’identificazione univoca del mover, monitorando così i dati del processo e lo stato in cui si trovano tutti i singoli carrelli. Ciò apre ai progettisti, nonché agli utilizzatori finali, nuove possibilità, poiché amplia le funzionalità tipiche di XTS con innovative ulteriori capacità di attuazione e di misura, dischiudendo nuove inimmaginabili opportunità di gestire flessibilmente la produzione in lotti unitari.
Controllo via software e tracking dei mover in tempo reale
Ciascun mover può essere controllato indipendentemente dagli altri e con una libera e specifica dinamica per il trasporto del relativo prodotto sul percorso assegnato. Essendo associate al singolo mover, le dinamiche di movimentazione possono essere modificate ‘al volo’ in qualsiasi istante in base alle specifiche esigenze. Se necessario, i mover possono essere sincronizzati anche con sequenze di processo esterne, nonché è possibile dare vita a formazioni di gruppo o a buffer mobili costituiti da un numero qualsiasi di mover. A livello di sistema, i singoli mover sono mappati come normalissimi servoassi. Le funzioni di controllo del movimento, gestite via TwinCAT, vanno comunque ben oltre le classiche funzionalità motion e permettono la gestione di funzionalità evolute e di alto livello, come l’accumulo automatico, la limitazione della forza centrifuga o la prevenzione di collisioni e strappi. Il plus di XTS è che tutte queste funzioni di movimento specifiche per l’applicazione possono essere facilmente implementate senza che la complessità del movimento porti a un’elevata complessità tecnica. Per gestire al meglio le esigenze applicative è ora possibile creare controlli HMI specifici. XTS HMI Control, generato a seguito dello sviluppo dell’applicazione, è automaticamente collegato a tutti parametri del processo, permettendo così di visualizzare in tempo reale le posizioni di ogni mover all’interno del sistema. Questa soluzione può essere integrata in modo semplice con altri controlli HMI, utilizzando perfino immagini animate. Gli utenti possono quindi creare rappresentazioni realistiche di sistemi completi, con uno sforzo di sviluppo minimo. Le informazioni fornite da XTS HMI Control aiutano inoltre a identificare “al volo” l’ubicazione di specifici mover qualora il sistema di trasporto sia particolarmente complesso: ciò sfruttando la gestione dei colori, evidenziando all’evenienza i mover di particolare interesse. Le possibilità non si esauriscono di certo qui, in quanto XTS HMI Control può essere utilizzato efficacemente per eseguire simulazioni, diagnostica e molto altro ancora. Il potenziale innovativo del sistema XTS, grazie alla tecnologia NCT, non si limita alle sequenze di movimentazione, anche se molto complesse. Il sistema, infatti, offre una grande capacità di adattamento, finemente scalabile in base alle esigenze del processo, ad esempio in relazione alla geometria, al numero di mover e allo specifico ambito applicativo. Componendo opportunamente più moduli XTS è possibile realizzare sistemi pressoché illimitati nella forma e nell’estensione ed espandendo le applicazioni attraverso la combinazione di più sistemi XTS, l’utilizzo avanzato delle funzionalità TwinCAT e l’integrazione della tecnologia robotica, ad esempio per implementare sistemi multirobot capaci di gestire prodotti tra loro diversi e in sequenze non preordinate. Se tutto questo viene utilizzato in modo coerente, insieme alle funzionalità di programmazione a oggetti, condition monitoring, sistemi di raccolta e analisi dati efficienti, collegati a cloud o data lake, con XTS e le funzioni NCT si realizzano impianti di produzione flessibili e smart.
Via i colli di bottiglia dei processi sequenziali
Uno degli aspetti più interessanti del sistema XTS NCT riguarda l’implementazione sul mover di attività specifiche, come la rotazione o la manipolazione di un prodotto al fine di presentarlo correttamente alla postazione di barcode scanning o al controllo qualità. L’impiego degli attuatori più adatti allo scopo trasforma quindi i mover in veri e propri sistemi mobili multifunzionali. La possibilità di assegnare profili di moto individuali a ciascun carrello e la capacità di eseguire lavorazioni direttamente a bordo mover rendono XTS un sistema che consente di progettare macchine concettualmente di gran lunga superiori alle classiche architetture produttive sequenziali, dove la stazione di lavorazione più lenta determina la velocità dell’intera produzione. XTS supera questa barriera, poiché gestisce i prodotti lungo il flusso produttivo caratterizzato da velocità variabili. Dopo una sosta prolungata in una stazione, la perdita di tempo può, ad esempio, essere assorbita accelerando il trasporto dei singoli prodotti tra le stazioni. I trasferimenti non devono infatti rispettare un ciclo comune, poiché le distanze e i profili di movimento sono tra loro indipendenti. Le stazioni di lavorazione sono perciò disaccoppiate fra loro. La lavorazione può anche essere eseguita in buffer mobili, mentre il flusso dei prodotti prosegue, con prestazioni di resa che, come è logico intuire, risultano notevolmente aumentate. Allo stesso tempo, il sottoprocesso più lento può essere duplicato o addirittura moltiplicato con l’XTS, aumentando di conseguenza la velocità di produzione e, quindi, le prestazioni complessive. Innumerevoli applicazioni possono trarre vantaggio dall’uso di un sistema come questo. Prendiamo ad esempio un caso reale, dove più sistemi di prelievo possono raccogliere indipendentemente gli ingredienti necessari per assemblare un menu completo all’interno di un kit pasto. I mover prelevano gli ingredienti dalle relative stazioni di carico e quindi li depositano ciascuno nella loro posizione predefinita. Ogni ingrediente può essere tracciato in modo completo, dal prelievo all’etichettatura. Il flusso produttivo risulta altamente flessibile: le personalizzazioni sono infatti libere, in quanto il cambio formato è gestito via software, il che permette di preparare kit pasto personalizzati addirittura in lotti unitari. Un aspetto molto importante da sottolineare è che gli elementi XTS con tecnologia NCT sono 100% compatibili con gli elementi XTS standard. La tecnologia NCT può quindi essere integrata nelle applicazioni XTS esistenti, consentendo di ampliare facilmente le applicazioni in tempi ridotti e con risparmio di risorse. Integrare la tecnologia NCT nei sistemi XTS esistenti consente di utilizzare solo i componenti essenziali, proteggendo così l’investimento e le applicazioni attuali. Ad esempio, in ambito farmaceutico, il sistema potrebbe essere facilmente ampliato con funzionalità NCT dedicate al controllo del riempimento e alla rotazione del flacone prima della sigillatura. Lo sforzo ingegneristico risulterebbe esiguo, in quanto gli attuatori sui mover, essendo anch’essi controllati tramite il software di automazione TwinCAT, sono parte del processo e possono quindi essere coordinati con precisione al microsecondo.
Assemblaggio e manipolazione di precisione
Con la sua innovativa architettura di automazione ad alte prestazioni, Beckhoff offre una piattaforma di automazione flessibile che, oltre a essere ideale per i processi di assemblaggio e movimentazione in cui velocità e precisione sono requisiti essenziali, può essere convenientemente utilizzata per offrire vantaggi anche ai processi ‘lenti’. In particolare, nelle applicazioni di assemblaggio e manipolazione il sistema XTS offre numerosi benefici, in primis la flessibilità, che apre diverse opzioni di movimentazione. Il cambio formato gestito via software si dimostra un impareggiabile alleato che riduce al minimo i tempi di fermo macchina per l’attrezzaggio. Inoltre, il profilo del moto personalizzato per ciascun mover consente di compensare le diverse tempistiche di attraversamento delle varie stazioni di assemblaggio, di fatto risolvendo il problema dei colli di bottiglia. Inoltre, la possibilità di eseguire lavorazioni e controlli di qualità direttamente sul mover aumentano l’efficienza e riducono l’ingombro macchina. Con la tecnologia NCT, il sistema XTS diventa quindi parte attiva del processo: manipolazione, assemblaggio, giunzione, saldatura, incollaggio, collaudo, dalle applicazioni più semplici fino a quelle più sofisticate. È molto significativo il caso di un’applicazione dove veniva richiesto un sistema di trasporto preciso per l’assemblaggio completamente automatizzato di moduli elettronici. Ebbene, la soluzione ottimale è stata trovata proprio nel sistema XTS NCT, che ha saputo garantire velocità, precisione e flessibilità estrema nei cambi di produzione.
XTS per il packaging: flessibilità, efficienza, ma anche sostenibilità
Con il suo sistema XTS, Beckhoff offre soluzioni di automazione che trovano nel packaging uno sbocco applicativo naturale, non solo perché in questo settore la velocità e la precisione sono essenziali, ma anche perché i produttori si stanno orientando su soluzioni che siano in grado di garantire efficienza e sostenibilità. In questo senso, la tecnologia Beckhoff si rivela molto conveniente per automatizzare tutti i processi di imballaggio, aprendo la strada a concetti di packaging completamente nuovi. In particolare, il sistema XTS combina i vantaggi del trasporto lineare con quelli di una soluzione rotativa. I prodotti possono essere movimentati indipendentemente l’uno dall’altro e, poiché sia i tratti rettilinei che le curve vengono attivamente utilizzati per il trasporto e la manipolazione, non ci sono ‘vuoti di processo’, il che rende l’applicazione complessivamente più veloce ed efficiente, con un ingombro della macchina che può risultare inferiore finanche del 50%. XTS rende dunque più efficienti i processi di confezionamento per via delle configurazioni specifiche e altamente personalizzate che è possibile implementare, grazie alla disponibilità di un vasto insieme di geometrie che sono liberamente componibili in base alle esigenze. La gestione totalmente software porta a cambi di formato estremamente rapidi e l’indipendenza dei carrelli, unitamente alla disponibilità delle funzioni di Track Management, offre la possibilità di eseguire attività di manutenzione senza interrompere il regolare flusso di produzione. Emblematico è il caso di un’applicazione che è stata recentemente realizzata in ambito di packaging, dove un’industria dolciaria sfrutta le potenzialità di due sistemi XTS per il confezionamento di package singoli e multipli. Il basso fabbisogno energetico, il design compatto e la performance in termini di velocità e flessibilità hanno portato l’azienda a ritenere XTS molto più vantaggioso rispetto ai sistemi convenzionali. Il cambio formato è pressoché immediato: le dimensioni dei prodotti, gli strati da impilare, il numero di unità per confezione, nonché il formato stesso della confezione possono essere variati semplicemente premendo un pulsante. Oltre a ridurre i tempi di fermo macchina pressoché a zero, l’applicazione di XTS ha permesso di migliorare le operazioni di manutenzione e pulizia, poiché tutte le componenti del sistema si trovano ora ergonomicamente collocate ad altezza uomo.
Batterie al litio: XTS NCT promette di abbattere i costi di produzione
Un interessante caso applicativo del sistema XTS NCT riguarda la produzione di batterie. Le batterie agli ioni di litio rappresentano oggi un elemento chiave per favorire lo sviluppo della mobilità elettrica: fino ad ora, il processo di produzione ha sempre rappresentato un costo che ha notevolmente impattato su quello delle auto elettriche. Attualmente, i ricercatori dell’Università di Berlino stanno comprendendo come sia possibile accelerare i processi di automazione pick-and-place che vengono utilizzati durante l’assemblaggio delle batterie agli ioni di litio abbattendone anche i costi. Nel nuovo approccio in corso di studio, il sistema XTS si è rivelato cruciale. Uno dei grossi problemi nella produzione delle batterie agli ioni di litio è che l’assemblaggio del composito elettrodo-separatore, costituito da molti strati, è piuttosto lento. Per la realizzazione di questo composito si applica un metodo di piegatura, denominato Z-Folding, che consiste nel prelevare anodi e catodi tagliati in fogli e inserirli in un separatore, costituito da un rotolo continuo che viene per l’appunto piegato a zeta al fine di mantenere separati i due elettrodi. Per realizzare queste strutture Zfolded sono necessarie molte operazioni di pick-and-place, che di norma vengono eseguite da robot o cinematiche speciali. Ogni elettrodo richiede dunque una specifica operazione di pick-and-place: si consideri che in una singola batteria da 50 Ah sono contenuti fino a 53 singoli elettrodi da 300 x 125 mm. L’operazione di Z-folding eseguita mediante il sistema XTS ha consentito ai ricercatori di sperimentare una significativa riduzione dei tempi. Nel sistema tradizionale, spingere eccessivamente la dinamica dei robot, con frenate e accelerazioni molto rapide, andrebbe a compromettere la precisione del processo, con ripercussioni qualitative che potrebbero determinare capacità ridotte delle celle o comparsa di cortocircuiti. I ricercatori hanno quindi sostituito il processo di pick-and-place robotizzato con un sistema di trasporto continuo dei materiali, elettrodi e strato separatore, gestito con XTS. I risultati ottenuti hanno dimostrato un sensibile aumento dell’efficienza, con il sistema che, se spinto al massimo, potrebbe addirittura superare del 150% le prestazioni dell’attuale processo. Ciò significa che potrebbe essere possibile produrre 250 celle nello stesso tempo che oggi viene impiegato per produrne 100. L’innovazione chiave in questo processo è la tecnica brevettata di piegatura a Z basata sul sistema di trasporto lineare XTS NCT, che i ricercatori hanno dotato di pinze rotanti. Due di questi sistemi, con un totale di dieci motori, garantiscono la piegatura continua del materiale e al tempo stesso il posizionamento preciso degli elettrodi nella cella. Gli elettrodi sono singolarmente disponibili sotto forma di pile di fogli, mentre il materiale isolante è alimentato in continuo sotto forma di nastro. Gli elettrodi vengono prelevati dalla pila e accelerati alla velocità del nastro per essere allineati con precisione e, quindi, fissati su di esso in modo alternato: il tutto in continuo. A questa fase preparatoria segue l’operazione di piegatura a ‘Z’, che viene effettuata mediante pinze speciali montate sui motori di due sistemi XTS interbloccati. I sistemi XTS sono montati in una struttura priva di vibrazioni che può essere integrata nella sequenza individuale di qualsiasi sistema di produzione di batterie. Nell’applicazione descritta, un totale di 15 servoazionamenti (AX8206, AX5125 e AX5206) e terminali aggiuntivi per servomotori EL7211 controllano le posizioni dei servomotori AM8000, che completano i due sistemi XTS, nelle varie unità di alimentazione. TwinCAT calcola la posizione di ogni mover in relazione agli altri in modo preciso e in tempo reale. Con questa soluzione, il tempo di piegatura è sceso da 1 a 0,7 secondi: ma ci sono ancora notevoli margini di miglioramento. In futuro i ricercatori dell’Università di Berlino stimano che si potrebbe scendere fino a 0,35 s per piega. Per gestire le pieghe in 0,7 s, i motori sono azionati a una velocità di circa 600 mm/s. Per raggiungere l’obiettivo di 0,35 s a piega è necessario aumentare la velocità a 1.000 mm/s. Poiché il sistema XTS è progettato per operare a velocità fino a 4 m/s come standard, ben si comprende come vi sia capacità sufficiente per accelerare ulteriormente il processo.
Un ulteriore passo avanti con XPlanar
Il concetto di movimentazione introdotto con XTS si è ulteriormente sviluppato con XPlanar, che permette di movimentare in modo indipendente ‘n’ mover fluttuanti, ovvero senza alcun contatto fisico con guide o supporti. Questo grazie alla presenza di un piano XY di riferimento, composto da una serie di piastrelle elettroniche tra loro liberamente interconnettibili, che generano un campo di forze elettromagnetiche capaci di sostenere dei pallet porta oggetti. Il sistema XPlanar non è vincolato ad alcuna struttura meccanica prestabilita (come binari o tracce), poiché lascia liberi i mover di procedere su percorsi alternativi e dinamicamente riconfigurabili per trasportare gli oggetti in modo flessibile. I mover possono essere movimentati lungo le dimensioni X-Y con velocità fino a 2 m/s e accelerazioni di 1 g, assicurando una ripetibilità di posizionamento pari a 10 µm. L’assenza di attrito rende il sistema silenzioso e immune alle problematiche di usura. Oltre a muoversi nel piano X-Y, le piastre possono sollevarsi e abbassarsi in verticale (asse Z) di 5 mm, inclinarsi di 5° su entrambi gli assi X e Y e ruotare di 360°, offrendo quindi 6 gradi di libertà, anche con una funzione integrata di pesatura opzionale. XPlanar offre differenti tipologie di mover: dalla taglia 113 x 113 mm, utilizzabile per movimentare carichi fino a 0,6 kg, alle taglie intermedie (155 x 155 mm e 155 x 235 mm) per spostare carichi più impegnativi (da 1,8 kg a 3,0 kg), fino alla taglia 235 x 235 mm, che ha una capacità di carico massima di 4,5 kg. Oltre alla movimentazione X-Y, le piastre fluttuanti sono in grado di ruotare di 360°. Questa funzionalità è anch’essa gestita, come tutto il resto del sistema, via software TwinCAT e aggiunge un ulteriore grado di libertà, che consente alla piastra di eseguire dei compiti durante lo spostamento con un orientamento modificato, in modo che i pezzi trasportati siano allineati per le successive fasi di lavorazione. La rotazione, eseguibile dinamicamente con una frequenza fino a 10 Hz, permette operazioni come la miscelazione di liquidi, l’ispezione a 360 gradi degli oggetti e il loro corretto orientamento davanti alle stazioni di marcatura. Inoltre, i motori possono allinearsi dopo la rotazione per le fasi di lavorazione successive. Disponibile in più opzioni costruttive – vetro, acciaio inox o film plastico – essendo immune da attriti e usure, XPlanar può trovare applicazione anche negli ambienti classificati come clean room, reparti di produzione alimentare e officine farmaceutiche.
Beckhoff Automation – www.beckhoff.com
Contenuti correlati
-
Ingegneria in cloud e assistenti AI nella suite di progettazione B&R
Alla fiera SPS di quest’anno a Norimberga, in Germania, B&R ha annunciato un importante aggiornamento della sua suite completa di software di progettazione e runtime. Con Automation Studio Code, B&R introduce un’esperienza di progettazione completamente nuova. La...
-
Additive manufacturing R-evolution al via con Energy Group e Stratasys
Il mondo dello sport può trarre grandi benefici dall’additive manufacturing: prototipazione, customizzazione, soluzioni per l’agonismo, produzione di singole parti funzionali e persino di interi lotti. Come? Affidandosi alla giusta tecnologia ma anche ai materiali più adatti ad...
-
Trasmissioni senza soluzione di continuità
Dispositivi quali switch, router e I/O per la comunicazione via industrial ethernet consentono di realizzare trasmissioni ‘dal campo al cloud’ senza soluzione di continuità Il mercato delle soluzioni di rete industriali è in rapida crescita, con un...
-
Advantech lancia il servizio di certificazione IEC 62443
Advantech lancia il servizio di certificazione IEC 62443, pensato per le esigenze di certificazione delle apparecchiature di edge computing in conformità alla norma IEC 62443 e agli standard correlati. Advantech offre una soluzione completa per aumentare la...
-
La nuova soluzione Emerson taglia costi dell’energia ed emissioni
Emerson ha lanciato la sua nuova soluzione Energy Manager, un’offerta di hardware e software pre-ingegnerizzati progettata per semplificare il monitoraggio dell’elettricità in ambito industriale con una configurazione rapida e un funzionamento intuitivo. La soluzione Energy Manager viene...
-
Ora disponibile da Altair PollEx per ECAD
Con Altair PollEx per ECAD, Altair offre agli ingegneri l’accesso gratuito a strumenti avanzati per la verifica dei circuiti stampati (PCB). I vantaggi con PollEx per ECAD PollEx per ECAD consente alle aziende di snellire i processi di...
-
Accordo di partnership fra Seco e NXP
Seco e NXP Semiconductors annunciano un importante traguardo nella loro collaborazione: la piattaforma software Clea di Seco sarà resa disponibile per tutti gli utilizzatori dei chip NXP e perfettamente integrata con la piattaforma di servizi EdgeLock 2GO...
-
Italian Machine Vision Forum 2024: 270 presenti a questa III edizione
Nella provincia bergamasca, tra i fiori all’occhiello della manifattura intelligente, si è svolto con ampia partecipazione il forum dedicato ai sistemi di visione industriale promosso da Anie Automazione e organizzato da Messe Frankfurt Italia. Il convegno: un’occasione per fare...
-
CAD per progettazione elettrica, SDProget presenta SPAC Automazione 2025
SDProget Industrial Software presenta SPAC Automazione 2025, la nuova e rinnovata versione del CAD professionale per la progettazione elettrica per l’automazione industriale. SPAC Automazione 2025 rende progettazione elettrica più potente e intuitiva, rispondendo alle nuove sfide di...
-
Wibu-Systems guiderà tour esclusivi a SPS 2024, mostrando CodeMeter in azione
Wibu-Systems ospiterà tour guidati esclusivi ad SPS 2024, l’evento principe nel campo dell’automazione, che si terrà a Norimberga, Germania, dal 12 al 14 novembre 2024. Tra gli innovatori ivi riuniti, Wibu-Systems dimostrerà come la sua tecnologia di...