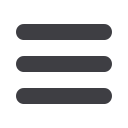
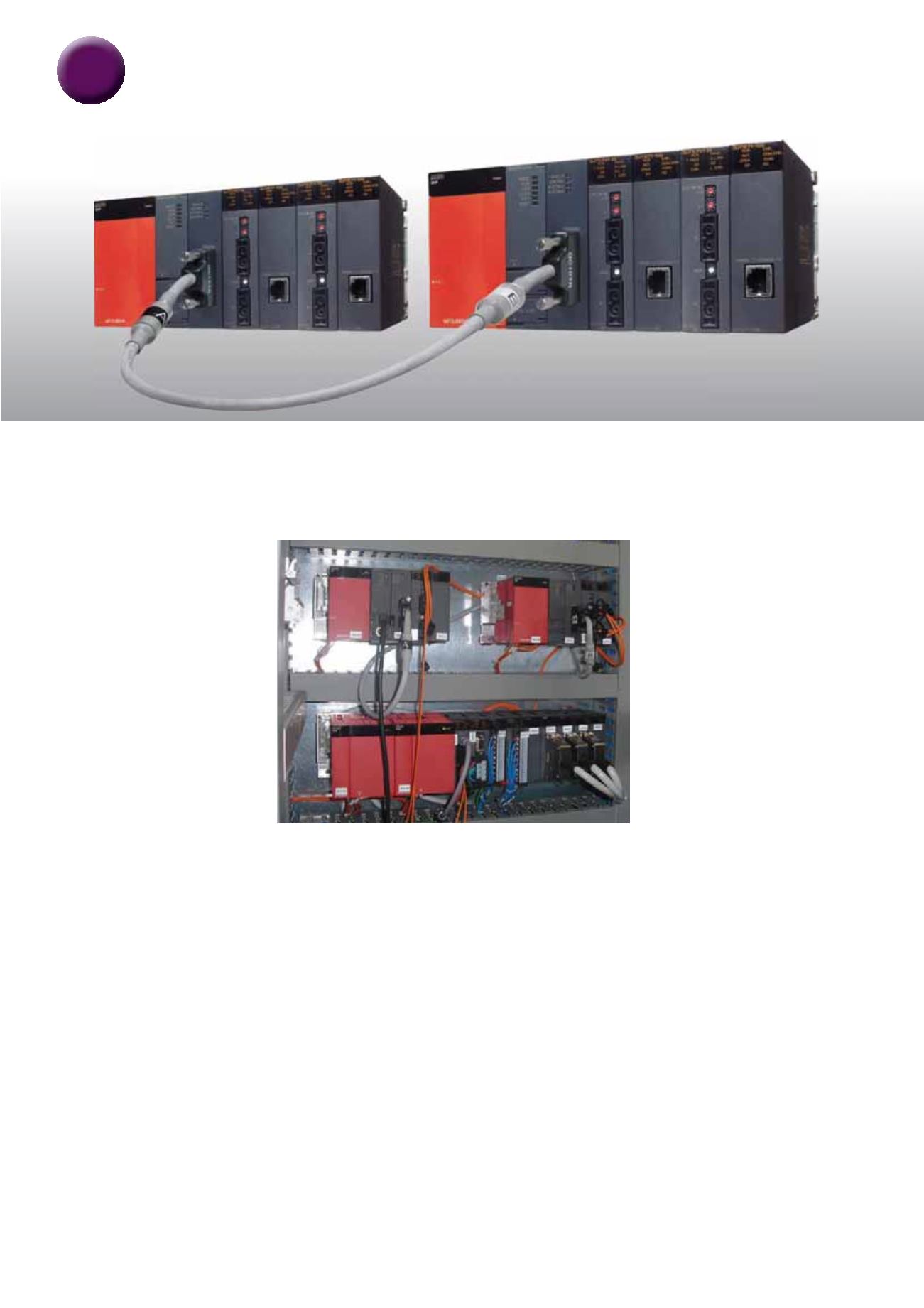
108
AUTOMAZIONE OGGI 381
SOLUZIONI SOFTWARE PER L’INDUSTRIA
S
SI
esperienze
corde sui rischi legati al malfunzionamento del controllo:
“Trasformatori e convertitori di potenza sono il cuore di
questo tipo di sistema perché se c’è un fermo macchina
il danno economico è notevole”. “Il PLC è responsabile di
tutta la parte di controllo e
protezione della macchina.
Ad esempio l’intero circuito di
raffreddamento è gestito tra-
mite il PLC. Le nostre macchine
sono raffreddate da acqua de-
ionizzata e acqua industriale
che circolano all’interno di uno
scambiatore industriale di ca-
lore. Attraverso canali analo-
gici acquisiamo le temperature
rilevate dalle numerose sonde
installate a bordo delle mac-
chine. Poi acquisiamo la mi-
sura di conduttività dell’acqua
deionizzata attraverso un’u-
scita analogica 4-20 mA, molto
importante per la sicurezza del
nostro circuito”. “Un sensore
PT 100 montato sulla parte alta
del quadro, che è la parte più
calda, ci consente di monitorare se la macchina sta andando
in sovraccarico o meno e se il circuito di raffreddamento sta
lavorando nella maniera appropriata. Abbiamo inoltre da ac-
quisire le temperature dai sezionatori attraverso schede elet-
troniche che si interfacciano con il PLC attraverso il semplice
ma affidabile protocollo Modbus. Tale protocollo viene anche
utilizzato per comunicare con i sistemi di controllo superiori
esterni per la scrittura dei riferimenti di corrente, di tensione
e l’acquisizione di tutte le misure di regolazione delle nostre
macchine, oltre al feedback di corrente e di tensione”. “Il PLC,
i regolatori digitali e l’analizzatore di rete corrono su proto-
collo Modbus e si interfacciano con un pannello operatore
GT16 della serie GOT1000, dove tutte le informazioni del
sistema vengono acquisite e visualizzate” continua Stucchi.
“In termini di programmazione, avevamo la necessità di un
tool semplice, ma allo stesso tempo potente per tutte le fasi
del progetto, dallo sviluppo fino al monitoring. Abbiamo
trovato il software di programmazione di Mitsubishi Electric
facile e intuitivo e ci ha consentito una rapida messa in ser-
vizio dell’impianto riducendo i
tempi di debugging”.
“Per venire incontro alle strin-
genti esigenze dell’applica-
zione del cliente, abbiamo
subito pensato di avvalerci
delle prestazioni della nostra
piattaforma di punta: iQ-Plat-
form. Grazie alla possibilità di
configurazione ridondata e
al supporto di I/O in una rete
in fibra ottica in architettura
a doppio anello è stato possi-
bile fornire al cliente la solu-
zione a massima disponibilità
richiesta. Da un punto di vista
dei costi, l’utilizzo di moduli
standard, utilizzabili anche in
sistemi per i quali le richieste
di ridondanza non sono così
stringenti, consente di ridurre
il numero delle parti di ricambio riducendo così il TCO del
sistema complessivo” conclude Antonio Gallo Toro, product
manager di Mitsubishi Electric.
A.O.: I raddrizzatori vengono utilizzati anche
nelle sottostazioni?
“Naturalmente sì, anche se sono di potenza completamente
diversa. Nelle applicazioni che abbiamo recentemente rea-
lizzato per Corea e Russia si parla di decine di MW, mentre
nelle sottostazioni siamo nell’ordine di qualche MW. Si tratta
poi di raddrizzatori non controllati dove non vi è la necessità
della tecnologia PLC per la gestione delle logiche di allarme,
di funzionamento e di raffreddamento” conclude Stucchi.
Mitsubishi Electric -
it3a.mitsubishielectric.comIl PLC, i regolatori digitali e l’analizzatore di rete corrono
su protocollo Modbus e si interfacciano con un pannello
operatore GT16 della serie GOT1000, dove tutte le
informazioni del sistema vengono acquisite e visualizzate
La richiesta di ridondanza nasce dal fatto che
l’impianto di raddrizzamento è il cuore dell’impianto industriale