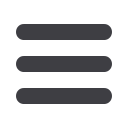
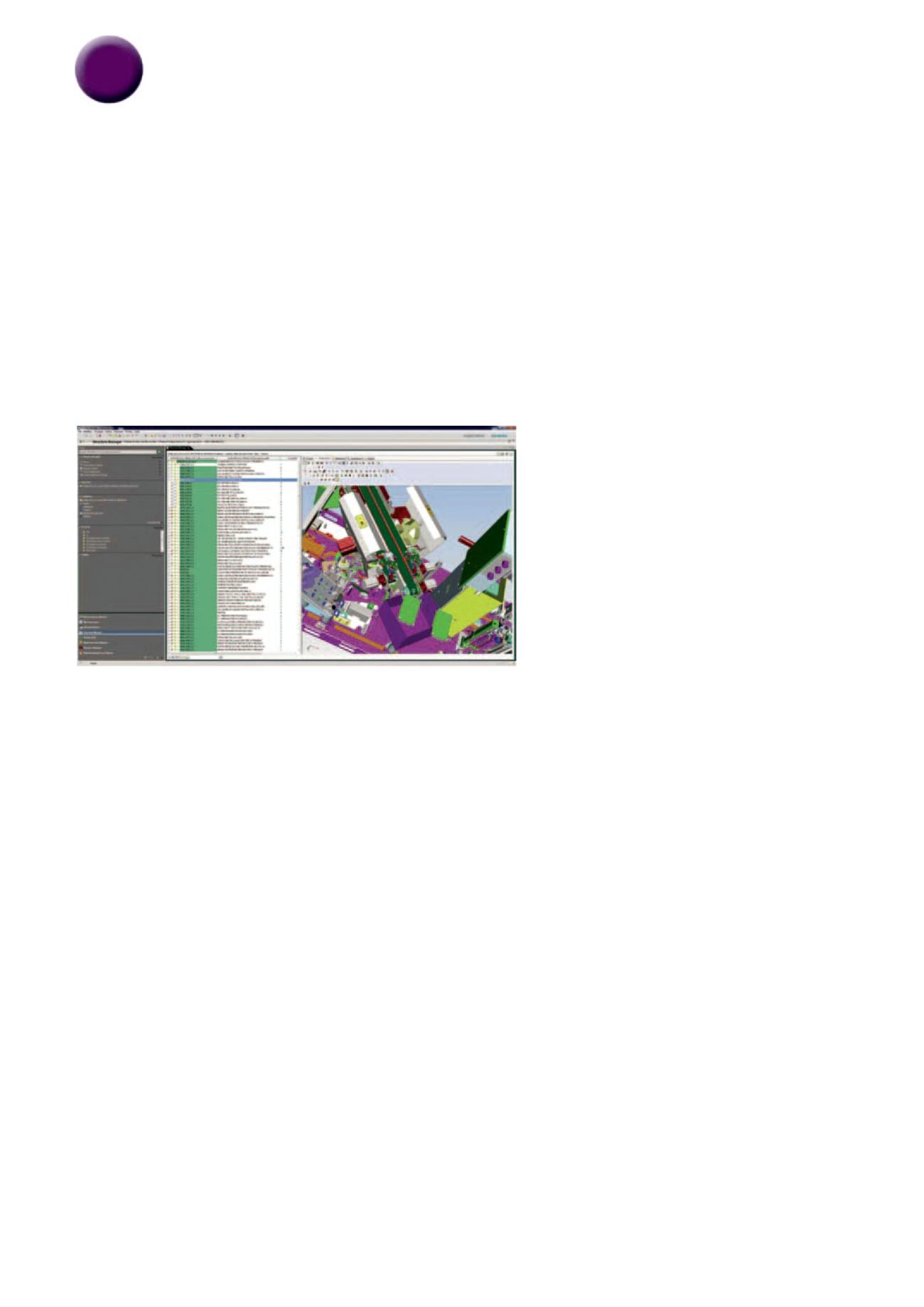
AUTOMAZIONE OGGI 398
SOLUZIONI SOFTWARE PER L’INDUSTRIA 109
dono come una volta molta sperimentazione e una messa
a punto accurata per poter funzionare 24 ore su 24, in am-
bienti difficili, polverosi, umidi e caldi, con temperature nelle
sale che possono salire fino a 48 gradi e disuniformità nell’ali-
mentazione di energia, con forti sbalzi di tensione”.
Le macchine sono tipicamente macchine operatrici, quindi
devono essere molto versatili e facili da regolare, perché
devono potere lavorare indifferentemente sia filati finissimi
e delicati, sia filati più grossi e grezzi. Le macchine fabbri-
cate da Savio hanno generalmente una testata di comando
a cui sono collegate numerose unità operatrici tutte uguali,
delle quali l’azienda produce circa 120 mila unità all’anno.
Queste unità richiedono robustezza, insensibilità alle varia-
zioni ambientali e all’accumulo di polvere, facilità di pulizia
e manutenzione, e devono essere utilizzate da personale
con scarsa formazione. “Per questo motivo i nostri quadri di
comando hanno interfacce in tutte le lingue e, soprattutto,
molte icone e immagini” dice Badiali. Il ciclo di sviluppo delle
macchine parte da specifiche di base già ben definite, frutto
della raccolta continua di dati e informazioni ricavate da di-
verse fonti; si esegue una prima progettazione che, oltre alle
verifiche dei nuovi concetti, analisi a elementi finiti (FEA) e
prove di laboratorio, porta a realizzare simulatori e prototipi
che vengono provati in-field per almeno sei mesi. I risultati
ottenuti permettono correzioni e messa a punto dei disegni
per arrivare poi a una pre-serie e a una serie definitiva. Oggi
la progettazione di tipo meccatronico consente possibilità di
modifiche in corso d’opera sconosciute 30 anni fa. Il cliente
trova normalmente tutte le risposte alle sue esigenze nella
gamma di offerta di Savio, oltre all’assistenza per redigere i
piani di lavoro, per definire il numero di unità necessarie e
gli ingombri in fabbrica. “Le richieste di personalizzazione
sono state via via incorporate nelle parti di produzione, così
che i progettisti del nostro ufficio tecnico intervengono solo
nel caso in cui ne siano richieste di nuove” sottolinea Badiali.
“Ma attualmente il 95% delle parti delle nostre macchine è
standard. Le macchine quindi abbisognano solo di essere
configurate secondo le esigenze del cliente”.
S
SI
esperienze
Strumenti per migliorare
Il ciclo di produzione attuale di Savio dura cinque settimane
(rispetto ai tre mesi di una volta), dall’ordine all’inizio della
fase di montaggio, che richiede un’ulteriore settimana.
L’obiettivo è stato raggiunto grazie al lavoro di standardiz-
zazione delle parti, supportato da strumenti tecnologici ade-
guati, fra cui progettazione a computer e gestione dei dati
di prodotto. “Fin dal 1985 abbiamo implementato strumenti
CAD e PDM idonei alle nostre esigenze di costruttori di mac-
chine meccaniche” racconta Badiali. “A noi serve una solu-
zione flessibile, per poter gestire le parti che costituiscono
le nostre macchine, quali lamiere, plastica, pressofusioni,
getti in ghisa, torneria, minuteria, componentistica,
pistoni, elettrovalvole...”. Nel 2010, in seguito alla
dismissione del pacchetto CAD/PDM in uso, la dire-
zione di Savio ha avviato una valutazione degli stru-
menti migliori disponibili sul mercato. Come riferisce
Badiali, l’obiettivo era individuare “un CAD flessibile
in grado di lavorare sia con il sistema parametrico
classico sia con un approccio senza storia, abbinato
a un PLM di buon livello sul quale replicare il nostro
sistema di organizzazione dei processi e dei flussi”.
Le esigenze di Savio sono piuttosto articolate, con
distinte base composte mediamente da 13 mila
componenti (che coprono tutte le alternative e gli
opzionali della macchina), mentre una singola mac-
china configurata ne utilizza circa 5.000. Ciascun
cliente sceglie la propria configurazione compilando
moduli che prevedono 40 tipi di scelta. L’azienda produce
otto tipologie principali di macchine per le quali, conside-
rando le macrocategorie e le sottocategorie, attualmente
esistono oltre 30 diversi configuratori.
Migrazione riuscita
Nella fase di software selection, i responsabili di Savio hanno
incontrato diversi fornitori, facendo cadere la scelta finale
su Prime Team e Tech Value, specializzate nello sviluppo di
soluzioni ad alto valore aggiunto in termini di tecnologia e
consulenza. Gli staff di Prime Team e Tech Value, con espe-
rienza pluridecennale nel settore del CAD e del PLM, hanno
proposto le soluzioni di Siemens PLM Software, Solid Edge
per la progettazione in 3D e Teamcenter per la gestione del
ciclo di vita delle macchine, e un progetto molto accurato,
come racconta Badiali. “Prime Team e Tech Value hanno pre-
sentato e sviluppato il progetto correttamente, rispettando
le nostre aspettative in termini di implementazione, migra-
zione e start-up”.
Con l’adozione di Solid Edge, Savio ha migrato tutto il pro-
prio patrimonio progettuale 3D e 2D all’interno di Solid Edge
e Teamcenter. “Con il software precedente eravamo limitati
ad alcune tipologie di assiemi perché il prodotto non reg-
geva la complessità delle nostre macchine” ricorda Badiali.
“Con l’aiuto prezioso di Prime Team e Tech Value abbiamo
convertito 450 mila file dal pacchetto 3D precedente a Solid
Un risultato è stata la maggiore flessibilità in ambito PLM e CAD con
conseguente riduzione dei tempi di modifica tecnica